Aluminum alloys are all around us, from the cars we drive to the planes we fly, the bikes we ride to the boats we sail. Two of the most widely used aluminum alloys are A356-T6 aluminum cast and 6061 aluminum. In this article, we'll explore the key differences between A356T6 aluminum cast vs 6061, from their compositions and manufacturing processes to their mechanical, thermal, and electrical properties. We'll also discuss their cost and common applications.
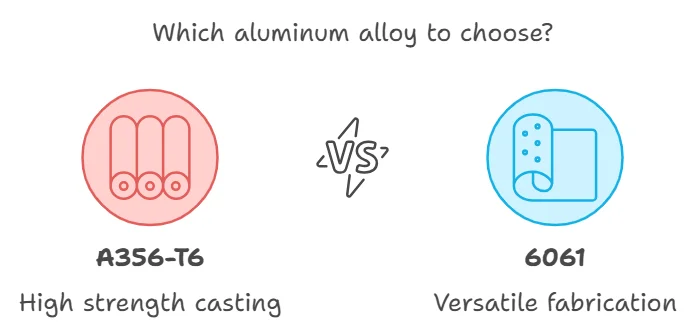
Composition

A356 and 6061 have different chemical compositions that affect their properties:
- A356 is an Al-Si-Mg alloy containing 6.5-7.5% silicon and 0.25-0.45% magnesium as the main alloying elements. It also has small amounts of iron (0.2% max), copper (0.2% max), zinc (0.1% max), titanium (0.2% max), and other elements (0.15% max total).
- 6061 is an Al-Mg-Si alloy containing 0.8-1.2% magnesium and 0.4-0.8% silicon as the main alloying elements. It also has 0.7% max iron, 0.15-0.4% copper, 0.04-0.35% chromium, 0.25% max zinc, 0.15% max titanium, and 0.15% max manganese.
The higher silicon content in A356 improves its castability, while the balanced magnesium and silicon in 6061 enable precipitation hardening. A356 has tighter limits on impurities like iron and copper compared to 6061.
Manufacturing
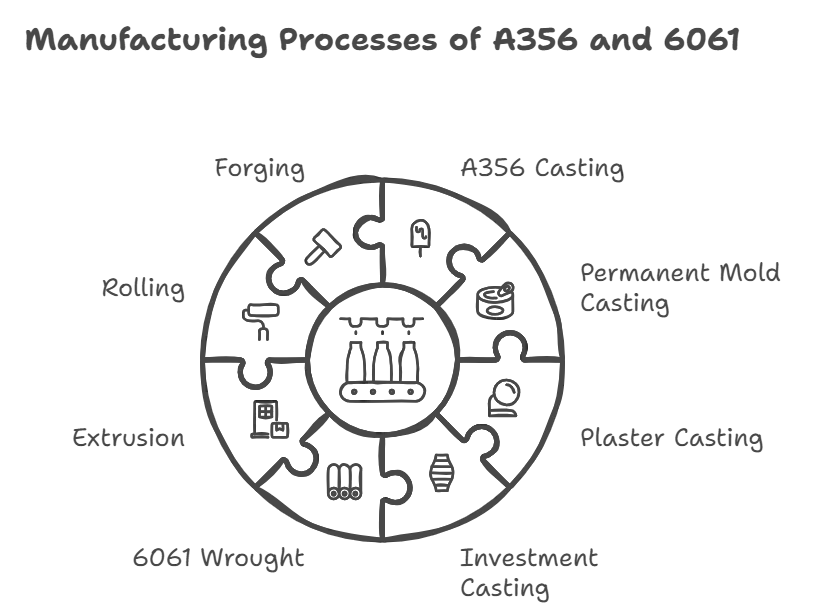
A356 and 6061 are produced via different manufacturing routes:
Manufacturing process of A356
A356 is a casting alloy that is shaped by pouring molten metal into a mold cavity. Common casting methods for A356 include:
- Permanent mold casting (gravity die casting): Molten A356 is poured into a reusable metal mold and allowed to solidify. This method is suitable for producing parts up to 10 kg with good surface finish and mechanical properties. It has a relatively low pouring rate but utilizes gravity efficiently.
- Plaster casting: A plaster mold is made around a pattern (usually rubber) and baked to remove moisture. Molten A356 is then poured into the cavity. This method allows for complex parts with minimum 1.5mm wall thickness. The plaster molds are single-use but inexpensive.
- Investment casting: A ceramic shell is made around a wax pattern that is melted out before pouring. This method can produce complex parts up to 1000 lbs with excellent surface finish and dimensional accuracy. The ceramic shells are single-use.
Manufacturing process of 6061
6061 is a wrought alloy that is hot worked into shape by processes like:
- Extrusion: A 6061 billet is preheated to 400-500°C, coated with lubricant, then pushed through a steel die with the desired cross-section. Extrusion can produce long lengths of complex hollow and solid profiles. The extrusions are cooled, stretched and cut to length.
- Rolling: 6061 slabs are hot rolled on a reversing mill and coiled. The coils are then cold rolled to thinner gauges. Rolling produces 6061 sheet and plate.
- Forging: 6061 is heated to 360-520°C then hammered or pressed between dies into the desired shape. Forging can produce solid parts with high strength.
The choice between A356 casting and 6061 wrought product depends on the part complexity, production volume and property requirements. A356 is used for complex shapes that are difficult or uneconomical to machine from wrought 6061. 6061 wrought products have more consistent properties and are used for simpler shapes.
Heat Treatment

Both A356 and 6061 aluminum alloys are strengthened by precipitation hardening heat treatments, but the specific processes differ due to their different compositions and manufacturing routes.
A356-T6 Heat Treatment
A356 castings are heat treated to the T6 temper using the following steps:
- Solution Treatment: The casting is heated to 540°C (1000°F) and held at this temperature for 12 hours. This allows the Mg and Si alloying elements to fully dissolve into solid solution in the aluminum matrix.
- Quenching: The casting is rapidly quenched, typically in water, to room temperature. This step retains the alloying elements in a supersaturated solid solution.
- Artificial Aging: The casting is reheated to 155°C (310°F) and held at this temperature for 3-5 hours. During this step, finely dispersed Mg2Si precipitates form throughout the aluminum matrix, significantly increasing strength and hardness.
The precipitation of Mg2Si is the main strengthening mechanism in A356-T6. The solution treatment spheroidizes the eutectic silicon particles, improving ductility. Quenching preserves the supersaturated solid solution, while artificial aging forms the strengthening precipitates.
6061-T6 Heat Treatment
6061 wrought products are heat treated to the T6 temper using a similar process:
- Solution Treatment: The alloy is heated to 530°C (985°F) and held at this temperature for 1 hour per inch of thickness. This fully dissolves the Mg2Si precipitates into solid solution.
- Quenching: The part is quenched, typically in water, to room temperature to retain the alloying elements in supersaturated solid solution. Quenching must be rapid enough to avoid precipitation during cooling (>140°C/min for 6061).
- Artificial Aging: The alloy is aged by heating to 160-190°C (320-375°F) for 8-18 hours, depending on thickness. This causes precipitation of fine Mg2Si particles that strengthen the matrix.
In 6061-T6, the main strengthening precipitate is also Mg2Si. The solution treatment temperature is lower than for A356 due to the lower Si content. Quenching rate is critical to avoid precipitation at grain boundaries. Artificial aging parameters are adjusted to optimize strength and corrosion resistance.
In summary, both A356-T6 and 6061-T6 are strengthened by precipitation of Mg2Si through solution treatment, quenching and artificial aging. However, the specific temperatures and times are tailored to each alloy's composition and product form to achieve a balance of strength, ductility and toughness. The T6 temper provides the highest strength for both alloys.
Mechanical Properties
The mechanical properties of A356-T6 and 6061-T6 aluminum are similar, but with some key differences:
Property | A356-T6 | 6061-T6 |
---|---|---|
Tensile Strength | 310 MPa (45 ksi) | 310 MPa (45 ksi) |
Yield Strength | 275 MPa (40 ksi) | 276 MPa (40 ksi) |
Elongation at Break | 6% | 12% |
Modulus of Elasticity | 72.4 GPa (10.5 x 10^6 psi) | 68.9 GPa (10.0 x 10^6 psi) |
Poisson's Ratio | 0.33 | 0.33 |
Shear Modulus | 27 GPa (3.9 x 10^6 psi) | 26 GPa (3.8 x 10^6 psi) |
Shear Strength | 200 MPa (29 ksi) | 207 MPa (30 ksi) |
Fatigue Strength | 130 MPa (19 ksi) at 5 x 10^8 cycles | 96.5 MPa (14 ksi) at 5 x 10^8 cycles |
Fracture Toughness | 25 MPa-m^1/2 | 29 MPa-m^1/2 |
Hardness | 80 HB | 95 HB |
- A356-T6 and 6061-T6 have comparable tensile and yield strengths, but 6061-T6 has significantly higher ductility (elongation at break).
- A356-T6 has slightly higher stiffness (modulus of elasticity) than 6061-T6.
- A356-T6 exhibits better fatigue strength than 6061-T6, but lower fracture toughness.
- 6061-T6 has higher hardness than A356-T6.
The differences in properties arise from the different compositions and microstructures of the two alloys:
- A356 has higher silicon content (7%) which forms a hard, brittle eutectic phase that increases strength but reduces ductility compared to 6061 (0.6% Si).
- The T6 heat treatment in A356 produces fine Mg2Si precipitates that strengthen the aluminum matrix, but also some coarse silicon particles that limit ductility.
- The T6 heat treatment in 6061 produces a high volume fraction of fine, coherent Mg2Si precipitates that provide a good balance of strength and ductility.
In summary, A356-T6 offers high strength and fatigue resistance at the expense of some ductility, while 6061-T6 provides a more balanced combination of strength and ductility. The choice between the two depends on the specific mechanical property requirements and design constraints of the application.
Thermal Properties
The key thermal properties of A356-T6 and 6061-T6 aluminum are:
Property | A356-T6 | 6061-T6 |
---|---|---|
Melting Range (Solidus - Liquidus) | 570-610°C (1060-1130°F) | 582-652°C (1080-1205°F) |
Specific Heat Capacity | 900 J/kg-K (0.22 BTU/lb-°F) | 896 J/kg-K (0.21 BTU/lb-°F) |
Thermal Conductivity | 150 W/m-K (87 BTU/h-ft-°F) | 167 W/m-K (97 BTU/h-ft-°F) |
Coefficient of Thermal Expansion | 21 µm/m-K (11.7 µin/in-°F) | 23.6 µm/m-K (13.1 µin/in-°F) |
Latent Heat of Fusion | 500 J/g | 395 J/g |
Maximum Service Temperature | 170°C (340°F) | 150°C (300°F) |
- A356 has a lower, tighter melting range compared to 6061 due to its higher silicon content (7% vs 0.6%). This improves its castability.
- The specific heat capacities are very similar for both alloys.
- 6061-T6 has about 11% higher thermal conductivity than A356-T6. Higher silicon in A356 reduces thermal conductivity.
- A356-T6 has a lower coefficient of thermal expansion than 6061-T6. Silicon reduces expansion while magnesium increases it.
- A356 has a higher latent heat of fusion than 6061 (500 vs 395 J/g). More energy is needed to melt A356.
- A356-T6 can be used at slightly higher temperatures than 6061-T6 while maintaining its strength (170°C vs 150°C).
The differences in thermal properties arise from the different alloying elements in A356 (7% Si, 0.3% Mg) compared to 6061 (0.6% Si, 1.0% Mg). The higher silicon in A356 reduces melting range, thermal expansion and conductivity, while increasing latent heat. This makes A356 well-suited for casting complex shapes. The balanced composition of 6061 provides good thermal conductivity for heat transfer applications.
Corrosion Resistance
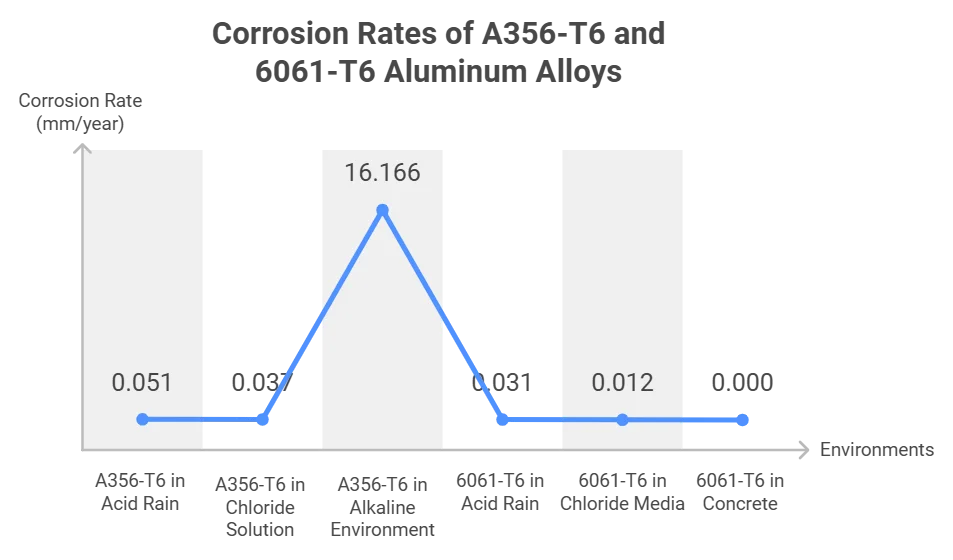
Both A356-T6 and 6061-T6 aluminum alloys have good corrosion resistance, but there are some differences:
- A356-T6 has excellent corrosion resistance in general atmospheric conditions and many chemical environments. The high silicon content (7%) in A356 promotes the formation of a protective oxide layer that resists corrosion. Studies show that A356-T6 has a corrosion rate of 0.051 mm/year in simulated acid rain and 0.037 mm/year in chloride solution.
- 6061-T6 also exhibits very good corrosion resistance due to the balanced magnesium and silicon content that enables stable passivation. It performs well in outdoor, marine and industrial environments. Tests indicate that 6061-T6 has a corrosion rate of 0.031 mm/year in acid rain and 0.012 mm/year in chloride media, slightly better than A356-T6.
- However, 6061-T6 is more susceptible to stress corrosion cracking (SCC) than A356-T6, especially in the short-transverse direction in wrought products. The T6 temper increases the SCC sensitivity of 6061.
- In the alkaline environment inside concrete (pH 12-13), A356-T6 shows poor corrosion resistance with a high corrosion rate of 16.166 mm/year due to the reactivity of aluminum in alkaline media. In contrast, 6061-T6 remains passive in concrete pore solution and is suitable for reinforcement.
Therefore, both alloys have good general corrosion resistance, with 6061-T6 being slightly better. However, A356-T6 is less prone to SCC and not suitable for concrete, while 6061-T6 can be used in concrete but is more susceptible to SCC.
Weldability
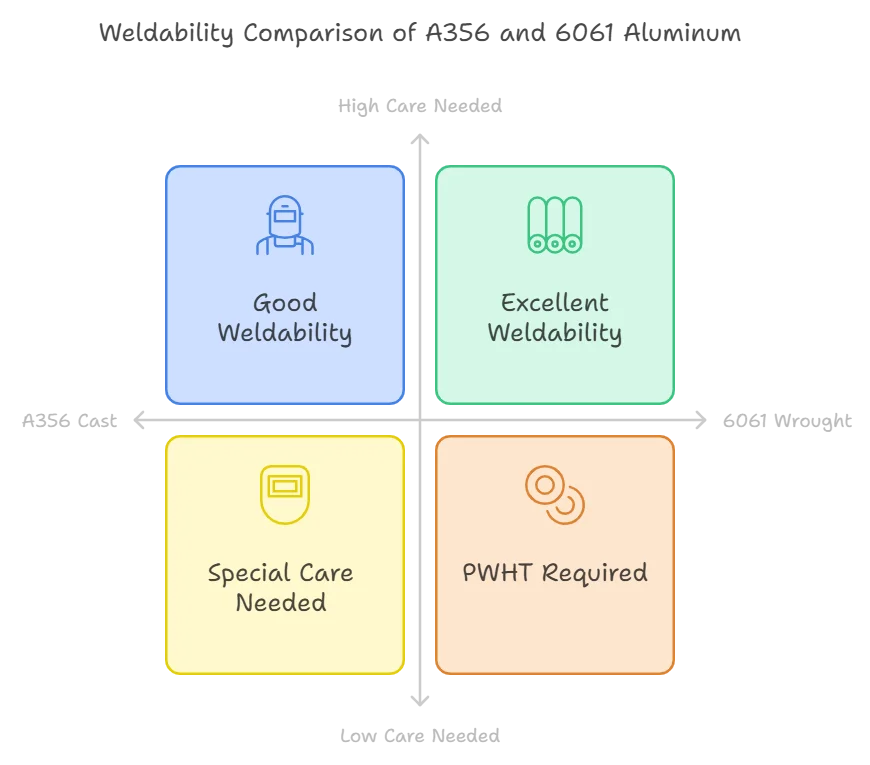
The weldability of A356 cast aluminum and 6061 wrought aluminum also differs:
- A356 castings have good weldability and can be welded using various processes like GTAW (TIG), GMAW (MIG) and SMAW. The high silicon content increases fluidity and reduces hot cracking susceptibility. However, the porosity in castings can lead to weld defects if not controlled.
- 6061 wrought products have excellent weldability and are among the most weldable aluminum alloys. They can be easily welded by GTAW, GMAW, and SMAW using 4043 or 5356 filler. The balanced Mg-Si content minimizes the risk of hot cracking and solidification cracking.
- When welding A356 castings to 6061 wrought parts, special care is needed due to the differences in thermal properties and solidification behavior. Using filler metals like 4043 or 4047 that are compatible with both base metals is recommended. Preheating the casting and controlling the welding heat input are necessary to avoid cracking.
- Post-weld heat treatment (PWHT) is often required to recover the strength of the weld zone in both A356 and 6061. Solution treatment followed by aging (T6 temper) is commonly used. The PWHT parameters need to be adjusted based on the alloy and section thickness.
In summary, 6061 wrought alloy has better overall weldability than A356 castings. Welding A356 to 6061 requires proper filler selection and process control to avoid defects. PWHT is necessary for both alloys to restore weld strength.
Electrical Properties
The key electrical properties of A356-T6 and 6061-T6 aluminum are:
Property | A356-T6 | 6061-T6 |
---|---|---|
Electrical Conductivity (Equal Volume) | 40% IACS | 43% IACS |
Electrical Conductivity (Equal Weight) | 140% IACS | 140% IACS |
Electrical Resistivity | 4.3 x 10^-6 ohm-cm | 4.0 x 10^-6 ohm-cm |
- 6061-T6 has slightly higher electrical conductivity by volume (43% IACS) compared to A356-T6 (40% IACS). IACS is the International Annealed Copper Standard, where 100% IACS represents the conductivity of pure copper.
- However, on an equal weight basis, both alloys have the same electrical conductivity of 140% IACS. This is because they have very similar densities (2.67 g/cm^3 for A356 vs 2.70 g/cm^3 for 6061).
- The electrical resistivity, which is the reciprocal of conductivity, is 4.3 x 10^-6 ohm-cm for A356-T6 and 4.0 x 10^-6 ohm-cm for 6061-T6. Lower resistivity indicates higher conductivity.
The small difference in electrical properties arises from the different alloying elements in A356 (7% Si, 0.3% Mg) compared to 6061 (0.6% Si, 1.0% Mg). Higher silicon content in A356 slightly reduces its conductivity compared to 6061.
So, 6061-T6 has marginally better electrical conductivity than A356-T6 on an equal volume basis, but is identical on an equal weight basis. Both alloys are good conductors, with conductivities 40-43% that of pure copper by volume and exceeding copper by 40% by weight due to their lower densities. The choice between them for electrical applications depends more on other properties like castability, strength, and cost.
Cost

A356-T6 and 6061-T6 aluminum alloys have different costs due to their distinct manufacturing processes and raw material requirements:
- A356 is a casting alloy, so its cost includes the expenses associated with the casting process, such as mold making, melting, pouring, and finishing. The raw materials for A356 (Al, Si, Mg) are relatively inexpensive.
- 6061 is a wrought alloy, so its cost includes the expenses of hot and cold working processes like extrusion, rolling, forging, and machining. The raw materials for 6061 (Al, Mg, Si, Cu, Cr) are slightly more expensive than A356.
In general, A356-T6 castings are less expensive than 6061-T6 wrought products of similar size and shape. This is because casting is a near-net-shape process that requires less machining and finishing compared to wrought products.
However, the cost advantage of A356-T6 diminishes for smaller quantities and more complex shapes that require intricate molds and more finishing work. 6061-T6 becomes more cost-effective for larger production runs of simpler shapes that can be efficiently extruded or machined.
The specific cost difference between A356-T6 and 6061-T6 varies depending on factors like part size, complexity, quantity, and supplier. As a rough estimate, A356-T6 castings can be 20-40% cheaper than equivalent 6061-T6 wrought parts.
Applications
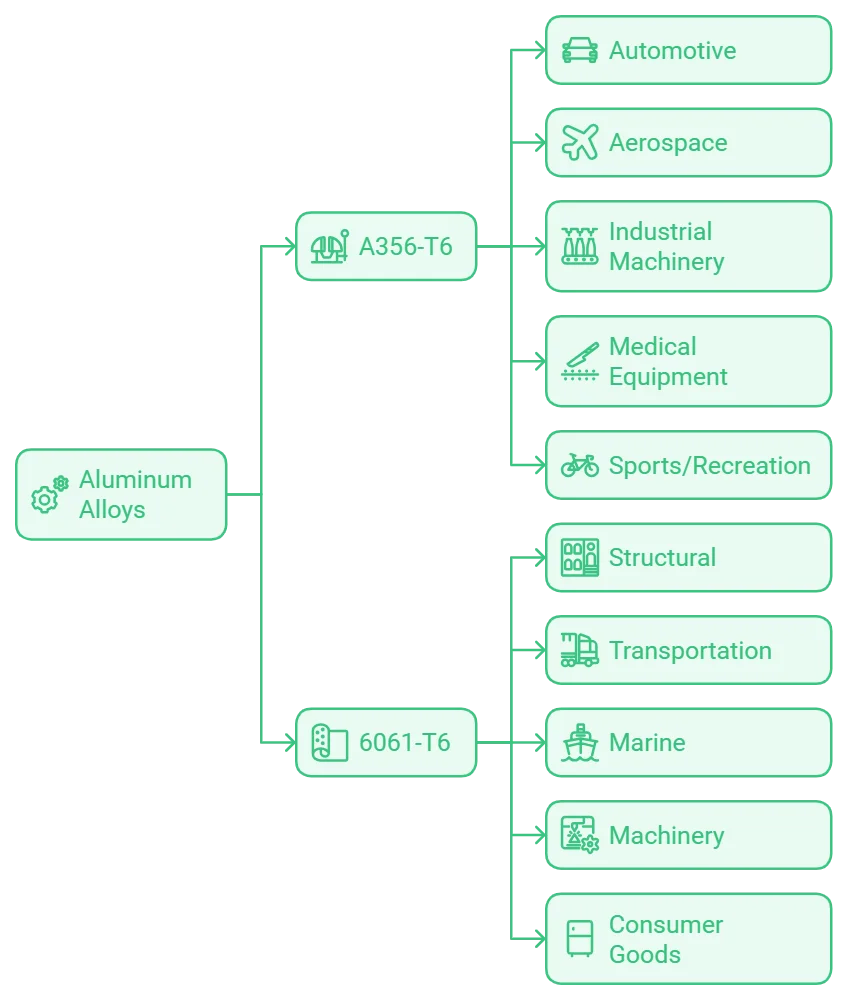
A356-T6 and 6061-T6 aluminum alloys are used in different applications based on their unique properties and manufacturing processes:
A356-T6 Applications
- Automotive: Engine blocks, cylinder heads, transmission cases, wheels, suspension components, steering knuckles, brake calipers.
- Aerospace: Aircraft fittings, fuel/hydraulic system components, control surface fittings, avionics housings, instrument enclosures.
- Industrial Machinery: Pump housings, impellers, valve bodies, gear boxes, motor housings, robotic components, machine tool parts.
- Medical Equipment: Surgical tool handles, orthopedic implant housings, dental equipment components, diagnostic device housings.
- Sports/Recreation: Bicycle frames, golf club heads, fishing reels, archery components, scuba diving equipment, pool ladder steps.
A356-T6 is chosen for these applications due to its high strength-to-weight ratio, excellent castability, good corrosion resistance, and fatigue strength.
6061-T6 Applications
- Structural: Bridges, towers, buildings, roof trusses, scaffolding, ladders, railings, highway signs, light poles.
- Transportation: Truck/trailer bodies, freight cars, ship hulls, gangways, superstructures, pipeline systems.
- Marine: Boat hulls, masts, booms, hardware, scuba tanks, fishing equipment, docks, marina infrastructure.
- Machinery: Food processing equipment, textile machinery, printing presses, injection molding machines, sawmill equipment.
- Consumer Goods: Appliances, furniture, cookware, computer hardware, sports equipment, luggage, ladders.
6061-T6 is selected for these applications because of its versatility, excellent formability, weldability, machinability, good strength, and corrosion resistance.
In short, A356-T6 is used for complex, high-strength castings in transportation, aerospace, industrial, and recreational sectors. 6061-T6 is a general-purpose alloy used for a wide variety of structural, transportation, marine, and consumer products that leverage its strength, workability, and corrosion resistance. The choice between them depends on the manufacturing process, design requirements, and cost considerations for the specific application.
FAQs about A356T6 Aluminum Cast vs 6061
What is A356-T6 aluminum cast?
A356-T6 is a cast aluminum alloy that contains primarily aluminum (91-93%), silicon (6.5-7.5%), and magnesium (0.25-0.45%). It undergoes a T6 heat treatment process involving solution treatment, quenching, and artificial aging to achieve high strength and hardness. A356-T6 is known for its excellent castability, corrosion resistance, and good mechanical properties, making it suitable for complex, high-strength castings in automotive, aerospace, and other industries.
What is 6061 aluminum?
6061 is a wrought aluminum alloy that contains primarily aluminum (95.85-98.56%), magnesium (0.8-1.2%), and silicon (0.4-0.8%) as the main alloying elements. It is a versatile, heat-treatable alloy known for its good strength, excellent corrosion resistance, high formability, and weldability. 6061 aluminum is widely used in various forms (sheets, plates, extrusions, etc.) for structural applications, transportation, marine, and consumer products. The most common temper is 6061-T6, which offers a balance of high strength and good workability.
What are the main advantages of using A356-T6 aluminum cast compared to 6061 aluminum?
A356-T6 aluminum cast offers several advantages over 6061 aluminum:
- Better castability, allowing for more complex and intricate shapes
- Lower density (2.67 g/cm3 vs 2.70 g/cm3), resulting in lighter weight parts
- Higher fatigue strength (90 MPa vs 96.5 MPa at 5x108 cycles)
- Slightly lower thermal expansion coefficient (21 vs 23.6 μm/m-K)
These properties make A356-T6 ideal for applications requiring lightweight, high-strength castings with good fatigue resistance, such as automotive and aerospace components.
In what situations would 6061 aluminum be preferred over A356-T6 aluminum cast?
6061 aluminum is often preferred over A356-T6 aluminum cast in situations where:
- Higher strength and hardness are required (6061-T6 has higher tensile, yield strength, and hardness)
- Better ductility and formability are needed (6061-T6 has 12% elongation vs 6% for A356-T6)
- Welding or machining is the primary manufacturing process (6061 has excellent weldability and machinability)
- Higher thermal and electrical conductivity are desired (6061-T6 has 11% higher thermal conductivity)
6061 is a versatile wrought alloy suitable for a wide range of structural applications, while A356-T6 is primarily used for castings.