Aluminum is a versatile metal used in various industries, from automotive to architecture. A common question among manufacturers and contractor is, can you powder coat aluminum? The answer is a resounding yes. Powder coating aluminum not only enhances its aesthetic appeal with a range of colors and finishes but also provides a durable, protective layer against corrosion and wear.
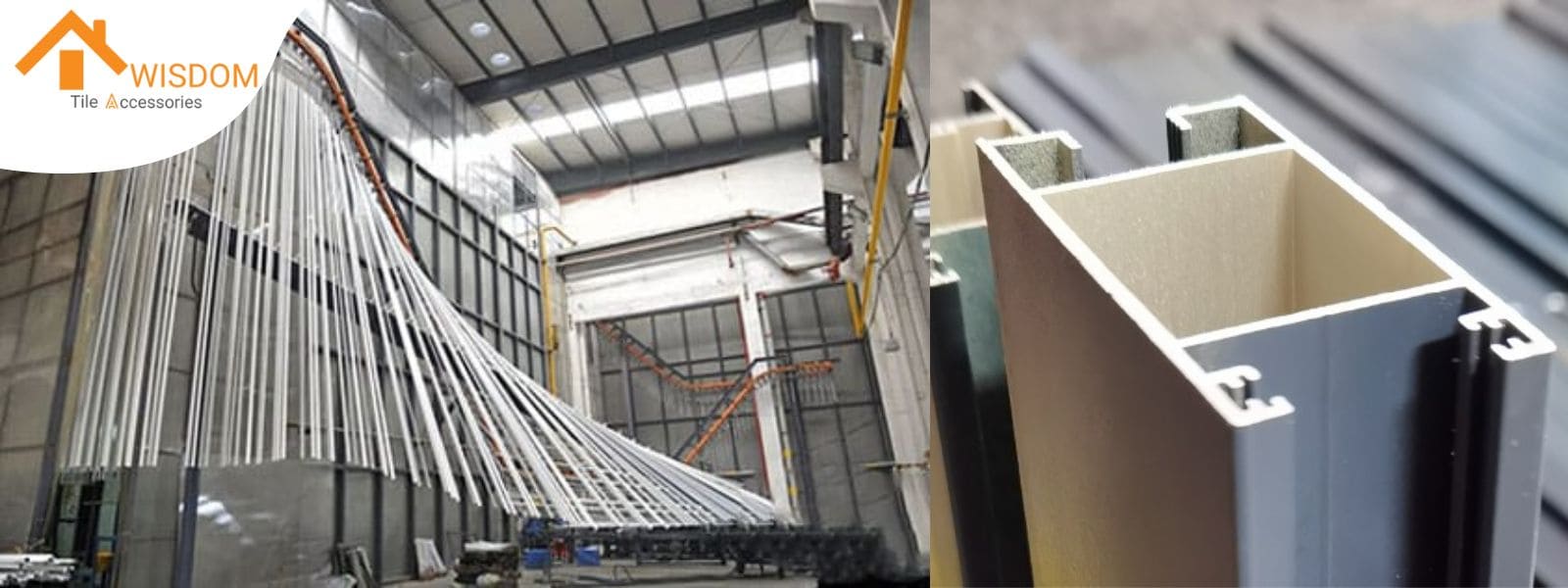
Understanding Aluminum Powder Coating
Powder coating is a dry finishing process that applies a free-flowing, dry powder to a surface, typically metal, and then cures it under heat to form a durable and protective layer. Unlike traditional liquid paint, which relies on solvents to keep the pigment and binder in liquid form, powder coating uses an electrostatic charge to adhere the powder to the surface. This process eliminates the need for solvents, making it environmentally friendly due to reduced volatile organic compound (VOC) emissions.
Type of Powder Coating | Key Features | Best Use |
---|---|---|
Polyester | Good flexibility, impact resistance | Indoor and outdoor |
Super Durable Polyester | Enhanced UV protection, long-lasting | Outdoor applications |
Epoxy | Excellent chemical and corrosion resistance | Indoor applications |
Urethane | Good chemical resistance, smooth finish | High-quality appearance |
Thermoplastic | Recyclable, durable | Thick coatings needed |
Thermoset | High temperature resistance, durable | Non-recyclable applications |
Can You Powder Coat Aluminum?
Yes, aluminum can be powder coated. Powder coating is a popular choice for finishing aluminum due to its ability to enhance durability, corrosion resistance, and aesthetic appeal. The process involves applying a dry powder to the aluminum surface and curing it under heat to form a protective and decorative layer. This method offers a wide range of color options and finishes, making it versatile for various applications.
Benefits of Powder Coating Aluminum
Enhanced Durability and Resistance to Wear
Powder coating provides a robust protective layer on aluminum surfaces, significantly enhancing their resistance to abrasion, chipping, and scratching. This makes powder-coated aluminum suitable for high-traffic or harsh environments, extending the life of the material and reducing maintenance costs.
Extensive Range of Color Options and Finishes
The powder coating process offers a diverse palette of colors and finishes, including matte, satin, gloss, and metallic textures. This flexibility allows for precise customization to meet specific aesthetic and functional requirements, making it ideal for architectural, automotive, and consumer product applications, such as powder coating aluminum tile trim.
Environmental Advantages
Powder coating is a more environmentally sustainable option compared to traditional liquid painting methods. It contains no solvents and releases negligible volatile organic compounds (VOCs) into the atmosphere. Additionally, the powder overspray can be efficiently collected and recycled, minimizing waste and reducing the environmental footprint.
The Main 5 Types of Powder Coatings used for Aluminum
1. Polyester Powder Coating
- TGIC and TGIC-Free: Polyester coatings are widely used due to their good mechanical properties, including flexibility and impact resistance. TGIC (triglycidyl isocyanurate) and TGIC-free (Primid) variants are available, with TGIC-free being more suitable for high-volume production due to its consistency.
- Super Durable Polyester: This is an enhanced version of polyester powder coating, offering greater UV protection and longer-lasting durability, making it ideal for outdoor applications.
2. Epoxy Powder Coating
- Known for its excellent chemical and corrosion resistance, epoxy powder coating is ideal for indoor applications. However, it does not perform well in outdoor environments due to its susceptibility to UV degradation.
3. Urethane Powder Coating
- Urethane coatings offer good chemical resistance and are suitable for environments where chemical exposure is a concern. They provide a smooth finish and are often used in applications requiring a high-quality appearance.
4. Thermoplastic Powder Coating
- These coatings can be melted and reformed, making them recyclable. They are durable and suitable for applications requiring thicker coatings.
5. Thermoset Powder Coating
- Thermosets undergo a chemical reaction when heated, forming a solid, durable coating that is resistant to high temperatures. However, they cannot be recycled once cured.
How Long will Powder Coating Last on Aluminum?
Powder coating on aluminum can last for a significant period, typically ranging from 15 to 20 years, and in some cases, up to 40 years. The longevity of the powder coating depends on several factors, including the quality of the surface preparation, the type of powder coating used, and the environmental conditions to which the coated aluminum is exposed.
Factors Affecting Longevity
- Surface Preparation: Proper surface preparation is crucial for ensuring the longevity of powder coating on aluminum. This involves cleaning the aluminum thoroughly to remove any debris, oils, or existing coatings, and creating a slightly roughened surface to enhance adhesion.
- Type of Powder Coating: Different types of powder coatings offer varying levels of durability. For example:
- Polyester and Polyurethane coatings are suitable for both indoor and outdoor applications and provide good flexibility and impact resistance.
- Epoxy coatings are highly durable indoors but do not weather well outdoors.
- Super Durable Polyesters are designed to maintain color and gloss for extended periods and provide better resistance to humidity and corrosion.
- Environmental Conditions: The environment plays a significant role in the lifespan of powder-coated aluminum. Exposure to extreme temperatures, humidity, and UV light can affect the durability of the coating. Powder coatings with UV-resistant additives are better suited for outdoor use.
- Application and Curing Process: The application process involves electrostatically applying the powder to the aluminum and then curing it in an oven. The quality of this process affects the coating's adhesion and durability.
So, when applied correctly and maintained under favorable conditions, powder coating can significantly extend the life and enhance the appearance of aluminum products, making it a popular choice for both industrial and consumer applications.
The Powder Coating Process for Aluminum
Surface Preparation and Cleaning
Proper surface preparation is critical for achieving optimal adhesion and finish quality. The aluminum substrate is cleaned to remove contaminants such as oils, dirt, and oxides. This can involve chemical treatments like alkaline cleaning or acid etching, as well as mechanical methods such as abrasive blasting or sanding to create a suitable surface profile.
Application of the Powder Coating
The powder coating is applied using an electrostatic spray deposition (ESD) process. In this method, the powder particles are electrically charged and sprayed onto the grounded aluminum surface. The electrostatic charge ensures uniform coverage and adhesion, even on complex geometries.
Curing Process and Temperature Requirements
Once the powder is applied, the coated aluminum is subjected to a curing process in a specialized oven. The curing temperature typically ranges from 180°C to 200°C (356°F to 392°F), depending on the specific powder formulation. During curing, the powder melts and chemically cross-links to form a continuous, durable film. This step is crucial for developing the coating's mechanical properties and ensuring long-term performance.
Powder Coating Aluminum vs Anodizing
The choice between powder coating and anodizing depends on the specific requirements of the application. Anodizing is preferred for its superior corrosion and wear resistance, making it suitable for high-traffic environments and applications requiring a durable finish. Powder coating, on the other hand, offers a broader range of colors and is more cost-effective, making it ideal for decorative purposes and applications where vibrant colors are desired.
Aspect | Powder Coating | Anodizing |
---|---|---|
Process | Electrostatic application of powder, followed by curing in an oven. | Electrochemical process forming an aluminum oxide layer. |
Durability | Good corrosion resistance; can wear and scratch more easily than anodizing. | Excellent wear, scratch, and corrosion resistance. |
UV Resistance | Very resistant to color fading, even when exposed to UV light. | Superior UV and weather resistance. |
Color Variety | Wide range of colors and textures available. | Limited to metallic colors; color consistency can be challenging. |
Environmental Impact | Environmentally friendly; no solvents use. | Environmentally friendly with proper electrolyte recycling. |
Cost | Generally more cost-effective than anodizing. | More expensive due to specialized equipment and processes. |
Applications | Suitable for vibrant colors and unique textures; used in outdoor equipment, automotive parts, and architecture. | Ideal for applications needing superior corrosion resistance, such as aerospace and electronics. |
FAQs about Powder Coating
What Metals Cannot Be Powder Coated?
Metals that cannot conduct electricity or withstand high curing temperatures are unsuitable for powder coating. This includes metals with non-conductive fillers and materials like rubber, plastic, and wood, which cannot endure the heat required for curing.
Is Sandblasting Necessary Before Powder Coating Aluminum?
Yes, sandblasting aluminum before powder coating is necessary to ensure proper adhesion. This process cleans the surface and creates a slightly rough texture, which helps the powder coating adhere more effectively, resulting in a durable finish.