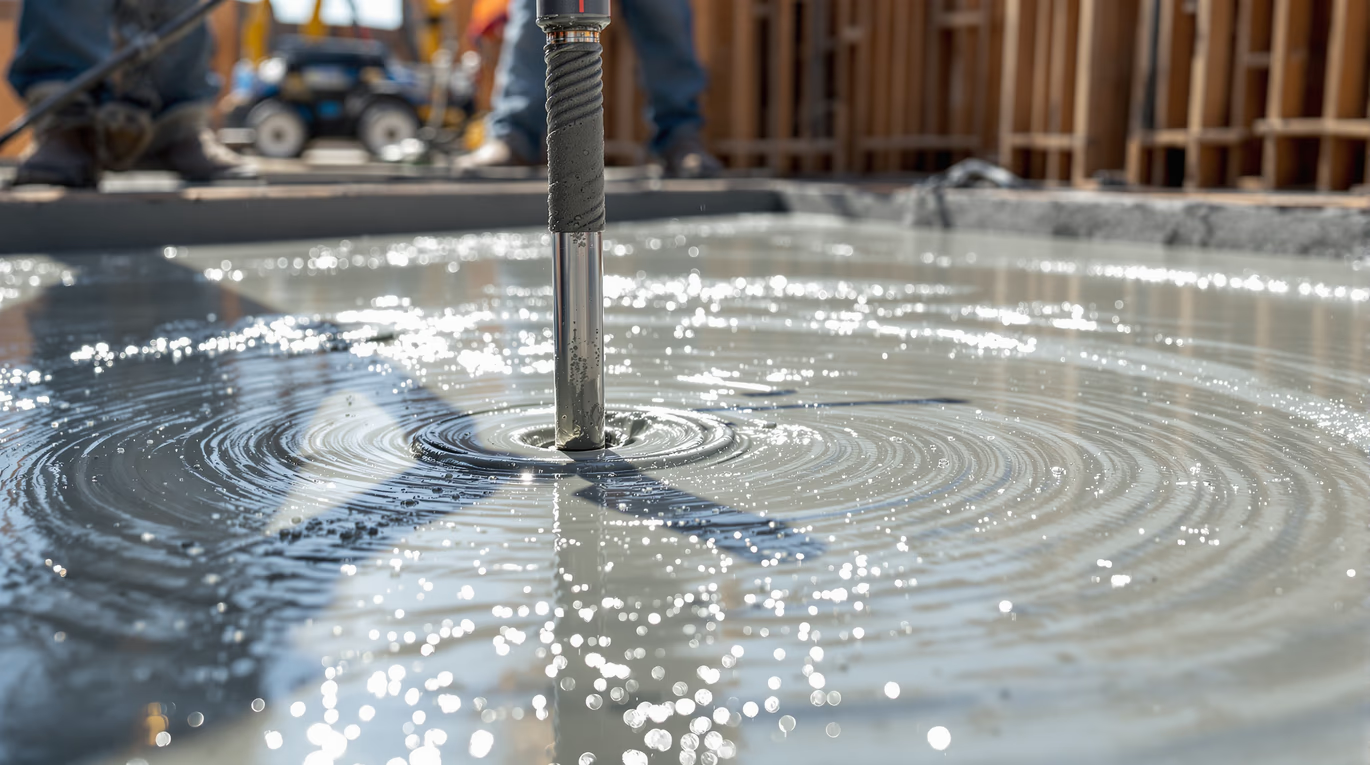
Many construction projects raise questions about do you have to agitate a concrete foundation. Your building's structural integrity depends on this vital process. The right concrete agitation creates a uniform mixture of cement, aggregates, and water that prevents separation and builds a stronger foundation.
The mixing consistency needs careful attention during concrete foundation installation. Poor agitation leads to visible separation, uneven setting, and foundation cracks. Large foundations and complex shapes make proper mixing even more significant. Ready-mix concrete arrives pre-agitated from delivery trucks, but some situations need extra mixing to get the best results.
This piece explores the importance of concrete foundation agitation and the work to be done to achieve maximum strength. You'll learn the right mixing techniques that ensure your foundation's durability.
Understanding Concrete Foundation Agitation
The chemical process of concrete setting starts with complex reactions between cement and water. Tricalcium silicate reacts faster with water and releases calcium ions and hydroxide ions. This reaction causes the pH to rise above 12. Calcium silicate hydrate then forms and becomes the main source of concrete strength.
Concrete agitation plays a vital role in keeping the mixture uniform throughout the setting process. The right agitation stops segregation, which prevents heavier components from sinking to the bottom and leaving a weaker top layer. The even distribution of water throughout the mixture ensures consistent hydration reactions. This process affects how calcium silicate hydrate crystals form, as they grow thicker over time and add to the concrete's overall strength.
Different concrete mixtures just need specific types of agitation based on their makeup and use. Trucks delivering ready-mix concrete keep it moving at low speed (about 2 rpm) to maintain an even mix. Transit-mixed concrete gets completely mixed in the truck during transport. Shrink-mixed concrete combines partial mixing at a stationary mixer before completing the process in a truck mixer.

The right timing of agitation leads to the best results. A dormancy period of one to three hours gives enough time to transport and place the concrete mixture. On top of that, it develops most of its strength within the first month, though this process continues slowly for years.
Some concrete mixtures need extra care with agitation. Large foundations and complex shapes often need more mixing to fill formwork completely. Concrete with lower water-cement ratios between 0.35 and 0.6 requires stronger agitation to achieve proper consolidation.
Essential Agitation Methods
The right agitation techniques are crucial to achieve the best concrete foundation strength. Construction companies use many methods, from simple manual approaches to advanced mechanical systems.
Mechanical agitation techniques
Truck-mounted rotating drum mixers are the backbone of mechanical agitation. These mixers work at two speeds - charging speed loads materials while agitating speed (less than 2 rpm) handles transport. The drum has helical blades that mix materials when spinning one way and release them when reversed.
Transit-mixed concrete needs the drum to spin at medium speed (8 rpm) for 70 revolutions during the drive to construction sites. Shrink-mixed concrete needs about thirty turns in the truck drum. A two-minute mix at mixing speed will complete the process.
Manual agitation procedures
Manual agitation methods still work well for smaller projects and specific uses, rather than being outdated. Hand tamping and spading help remove air voids and consolidate concrete properly around reinforcements. These methods work best with concrete depths of 6 inches or less.
Workers must follow systematic insertion patterns and controlled withdrawal rates. Industry standards say the vibrator should come out at about one inch per second. Each insertion should last about 10 seconds. This careful timing creates thorough consolidation without separating materials.
Modern agitation technologies
Smart monitoring and control systems now power advanced agitation systems. Modern concrete mixers come with:
- Automated calibration systems that keep material ratios exact
- Up-to-the-minute monitoring of mix consistency and temperature
- AI-driven analytics for predictive maintenance
- Remote operation options for better control
These tech advances have boosted mixing efficiency by a lot. Vibration monitoring systems use computerized sensors to track concrete consolidation throughout the pour. The equipment adjusts vibration frequency based on concrete consistency. Frequencies usually range between 0-100 Hz for the best results.
Smart technology in mixing operations has led to more consistent results. Automated systems keep precise control over agitation settings throughout the mixing process. This advancement has reduced common problems like segregation and air voids.
Critical Timing Factors
Time management plays a vital role in concrete foundation work. You need to know the exact timing requirements to get optimal strength and avoid structural problems.
Original mixing window
The type of mixing used determines the mixing window. Transit-mixed concrete needs the drum to rotate at mixing speed for about 70 revolutions. Shrink-mixed concrete needs about 30 drum rotations for complete mixing. The mixing time usually takes 1-3 minutes at standard mixing speed.
Transportation considerations
The time taken to transport concrete can make or break its quality. You have between 90 to 120 minutes from batching to complete discharge. Different regions have their own rules - US guidelines say 90 minutes, while UK standards allow up to 120 minutes.
Ready-mixed concrete follows these temperature-based setting times:
- At 100°F (38°C): 1-2/3 hours
- At 70°F (21°C): 6 hours
- At 40°F (4°C): 14 hours
Setting time variables
Temperature has a big effect on how fast concrete sets. The setting time changes a lot based on weather conditions. Concrete sets within 1-2/3 hours at 100°F, but needs about 11 hours at 50°F. When temperatures drop below 40°F, setting takes more than 14 hours.
The water-cement ratio ended up changing the setting duration. Studies show that higher ratios make the setting process slower. Under standard conditions, the concrete should not start setting before 45 minutes and must finish setting within 6.5 hours.
Weather conditions like humidity and wind speed also affect setting time. To name just one example, strong winds can dry the surface faster and cause the outer layer to set too early. Chemical admixtures, especially water reducers and retarders, can stretch the workability time beyond normal limits.
Regional Considerations
Regional differences are vital in determining concrete foundation requirements and agitation needs. The way concrete foundations need to be prepared and managed depends on climate conditions, local regulations, and geographical factors.
Climate impact on agitation needs
Environmental conditions affect concrete's durability and performance directly. Studies show that corrosion rates go up by 15% with every 2°C rise in temperature. Concrete foundations face several weather-related challenges:
- Temperature fluctuations affecting setting time
- Humidity levels impacting curing process
- CO2 concentration influencing carbonation
- Precipitation patterns affecting moisture content
- Wind conditions impacting surface drying
- Wave and tidal actions in coastal areas
Concrete structures in temperate zones break down differently than those in tropical regions. This means agitation requirements must change based on these regional climate variations to ensure proper concrete consolidation.
Local building codes and requirements
Building codes vary by a lot across regions and reflect local environmental conditions and construction practices. These codes set minimum requirements for concrete foundation durability and performance. Structures in coastal areas must meet extra specifications because of their exposure to marine environments.
The National Flood Insurance Program (NFIP) sets specific foundation requirements for buildings in flood-prone areas. Local jurisdictions might add stricter standards based on regional hazards. These rules often specify concrete mixing and placement procedures to maintain structural integrity.
Geographical challenges
Each location brings its own challenges for concrete foundation installation. Coastal regions face increased environmental stresses and just need special attention to foundation design and concrete mixing. The risk of carbonation-induced damage can rise by more than 16% in some regions, so concrete preparation and placement need careful planning.
Soil composition changes across regions and affects foundation requirements. Areas with highly reactive clay soils need particular attention to concrete consistency and placement techniques. The ground's reactivity determines the depth and spacing of edge and internal beams, which makes proper agitation essential for even concrete distribution.
We must build climate adaptation strategies into concrete foundation practices. Research proves that adding 10mm of cover thickness for carbonation-governed durability and 5mm for chloride-governed durability helps reduce climate change effects. These changes often require adjustments to standard agitation procedures to achieve the best concrete placement and consolidation.
Quality Control Measures
Quality control measures make sure concrete foundations are installed correctly through systematic testing and monitoring. A detailed testing protocol and proper documentation throughout construction helps quality assurance work better.
Testing concrete consistency
Several standardized procedures verify mix properties during concrete consistency testing. A pressure method test shows air content in fresh concrete and readings come directly from an adjusted gage. Density testing confirms proper mix proportions and helps calculate cementitious material content.
Tests need to happen within these timeframes:
- Slump and air content tests: Within 5 minutes of sampling
- Temperature measurements: Within 5 minutes of sampling
- Strength tests: Within 15 minutes of getting the sample
Monitoring agitation effectiveness
Mix uniformity observations and standardized tests help monitor concrete agitation. The Super Air Meter (SAM) test measures both total air content and air-void system quality effectively. Concrete quality is acceptable when a SAM number stays below 0.20 psi and total air content is more than 5%.
These parameters verify concrete mixing uniformity:
- Maximum variation in coarse aggregate content: 170 lb/yd³ between samples
- Mixing time: Maximum 150 revolutions at mixing speed
Documentation requirements
Detailed records of all testing procedures and results are essential parts of documentation. A weighmaster certificate with actual scale weights for batched ingredients must come with each concrete delivery. The certificate needs to show:
- Mix design identification
- Batch weights of all materials
- Time of batching
- Total water content
- Admixture quantities
Field teams should check if scales balance at zero load and look for signs of sluggishness or inaccuracy regularly. Temperature measurements taken throughout placement should be part of quality control documentation.
Each pair of test cylinders needs proper identification with:
- Contract number
- Sample identification number
- Date cast
- Method of field curing
- Age at which cylinder will be tested
Testing agencies must keep detailed records that show they follow ASTM C1077 standards and have certified testing technicians. ACI Concrete Laboratory Testing Technician Level I certification or equivalent is required for personnel who conduct laboratory acceptance tests.
A registered design professional hired by the Testing Agency must certify test results used for acceptance. Records should be kept for 3-5 years from delivery date for forensic purposes.
Conclusion
Strong concrete foundation agitation is vital for structural integrity and durability that lasts. Our detailed study revealed that successful concrete foundation work relies on multiple factors that must work together.
Today's agitation methods use everything from mechanical truck-mounted systems to advanced computer technologies to create the perfect concrete mixture consistency. The right agitation requirements depend on temperature, timing, and where you're working. Teams use standardized testing and careful documentation as quality control measures to make sure foundations meet all standards.
The technology behind concrete agitation keeps getting better. Studies show that when teams pay close attention to mixing consistency, environmental conditions, and timing, they substantially reduce common problems like segregation and uneven setting. Each region's building codes and geographical challenges create unique requirements. This makes it vital to understand local variations.
Concrete foundation agitation needs both technical expertise and hands-on experience. The right agitation techniques form the foundation of strong, lasting structures that can handle time and environmental stress, whether you're working on large construction projects or smaller installations.
FAQs about Do You Have to Agitate a Concrete Foundation
Q1. Is concrete agitation necessary for a foundation?
Concrete agitation is essential for foundations as it ensures a homogeneous mixture, prevents segregation, and contributes to the overall strength and durability of the structure. Proper agitation creates a uniform distribution of materials, reducing the risk of weak spots and improving the foundation's integrity.
Q2. How long should concrete be agitated during the mixing process?
The duration of concrete agitation depends on the mixing method. For transit-mixed concrete, the drum should rotate for about 70 revolutions at mixing speed. Shrink-mixed concrete typically requires about 30 drum rotations. Generally, mixing time ranges from 1-3 minutes at standard mixing speed to achieve optimal consistency.
Q3. What factors affect concrete setting time in foundations?
Several factors influence concrete setting time, including temperature, water-cement ratio, and environmental conditions. Higher temperatures accelerate setting, while colder temperatures slow it down. The water-cement ratio affects consistency, and factors like humidity and wind speed can impact the curing process. Chemical admixtures can also extend workability time.
Q4. How do regional factors impact concrete foundation requirements?
Regional factors such as climate, local building codes, and geographical challenges significantly influence concrete foundation requirements. Climate affects durability and performance, while local regulations may dictate specific mixing and placement procedures. Soil composition and environmental stresses in different regions also necessitate adjustments in foundation design and concrete preparation.
Q5. What quality control measures are important for concrete foundations?
Key quality control measures for concrete foundations include testing concrete consistency, monitoring agitation effectiveness, and maintaining detailed documentation. Standard tests like slump and air content should be conducted within specific timeframes. Monitoring mix uniformity and using technologies like the Super Air Meter (SAM) help ensure proper agitation. Comprehensive documentation of all procedures, test results, and material specifications is crucial for quality assurance.