What is Aluminum Alloy Anodizing
Aluminum alloy anodizing is an electrochemical process that enhances the natural oxide layer on aluminum surfaces. This process involves submerging the aluminum in an acid electrolyte solution and applying an electric current.
The result is a durable aluminum oxide layer that is integrated with the base metal, providing enhanced corrosion resistance and wear resistance Unlike other surface treatments, anodizing does not add material on top of the aluminum; instead, it transforms the surface itself into a protective layer The anodized layer is porous, allowing for secondary processes such as coloring through dyes or sealing for additional protection.
This makes anodized aluminum highly versatile for various applications, including architectural components, automotive parts, and consumer products. The process is environmentally friendly and does not produce harmful by-products, making it a preferred choice in industries requiring durable and aesthetically pleasing finishes.
Understanding Anodizing
Anodizing is a controlled electrochemical process that modifies the surface of aluminum alloys to improve their properties. It involves immersing the aluminum in an acid electrolyte bath and passing an electric current through it. This process thickens the natural oxide layer on the surface, enhancing its durability and resistance to corrosion.
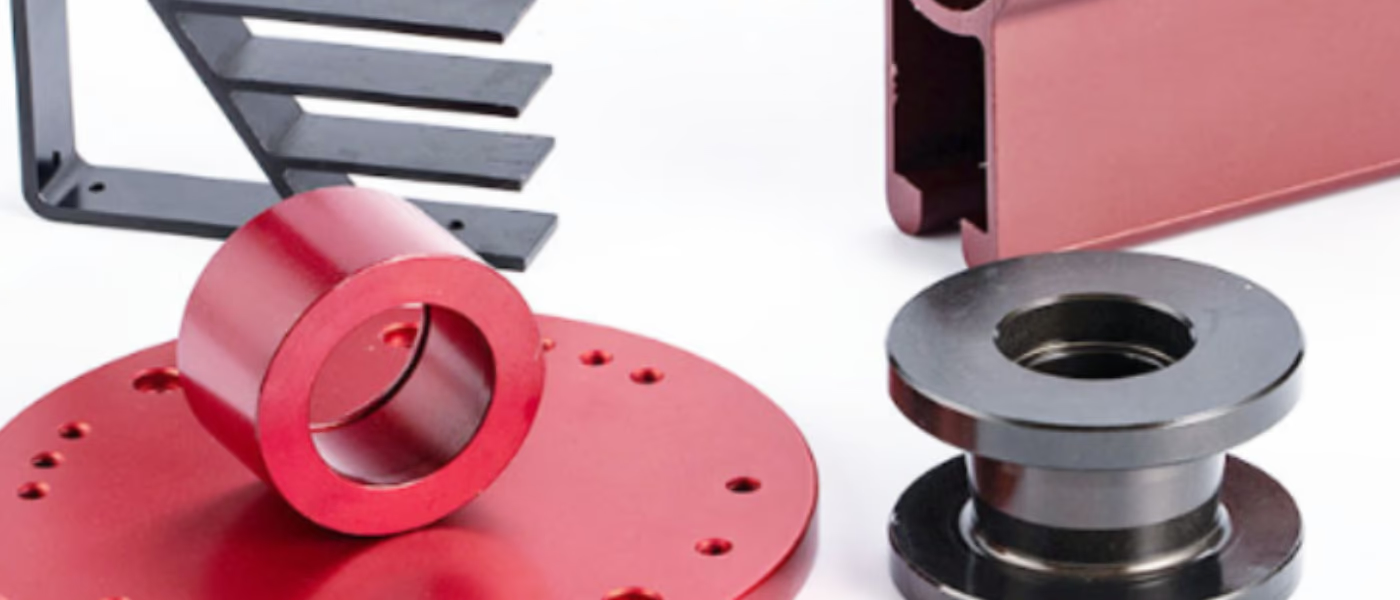
There are three primary types of anodizing:
Type I (Chromic Acid Anodizing):
Produces a thin, protective layer. It is often used in aerospace applications due to its ability to preserve tight tolerances.
Type II (Sulfuric Acid Anodizing):
The most common type, offering moderate thickness. It is suitable for a wide range of applications, including architectural and decorative uses.
Type III (Hardcoat Anodizing):
Results in a thicker, more robust coating. This type is ideal for heavy-duty applications where increased wear resistance is required.
Each type of anodizing is used for different purposes depending on the desired properties such as thickness, hardness, and colorability. The choice of anodizing type depends on the specific requirements of the application, balancing factors such as durability and aesthetics.
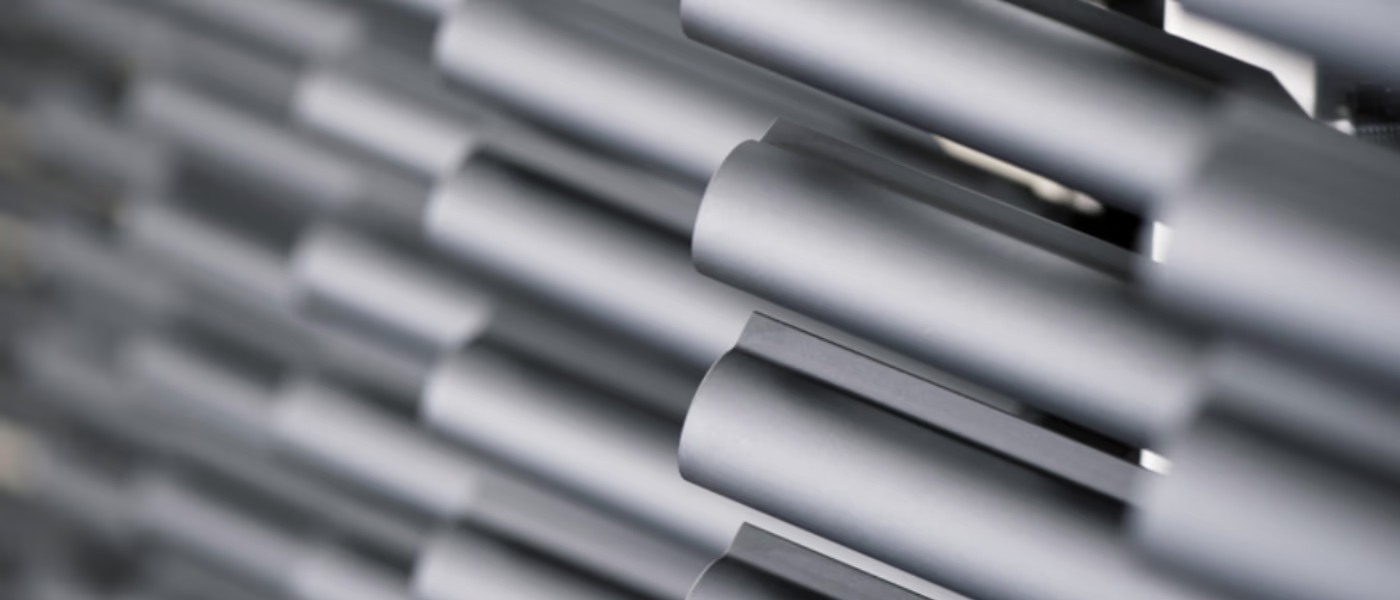
Specifications and Standards for Anodizing of Aluminum Alloys
Specifications for anodizing aluminum alloys are crucial for ensuring the quality and performance of anodic coatings. One of the most widely recognized specifications is MIL-A-8625, established by the United States Department of Defense.
This specification outlines requirements for anodic coatings on aluminum and its alloys, focusing on enhancing corrosion resistance, wear resistance, and paint adhesion. It includes guidelines for different types of anodizing, such as Type II (Sulfuric Acid Anodizing) and Type III (Hardcoat Anodizing). Type II coatings are typically used for general purposes and can be colored, while Type III coatings are thicker and more suitable for heavy-duty applications.
Another important specification is AMS 2472, which is extensively used in aerospace applications. It details the anodizing process conditions, quality assurance tests, and performance criteria necessary to achieve high durability and reliability. AMS 2472 emphasizes pre-treatment procedures, precise control of anodizing parameters, and rigorous quality control measures to ensure consistent coating performance.
Additionally, architectural applications often follow AAMA 611, which specifies performance requirements for anodized aluminum used in exterior environments. This specification includes tests for coating thickness, weight, and seal quality to ensure long-lasting finishes in architectural settings.
These specifications not only define the technical requirements for anodizing but also guide manufacturers in achieving consistent results that meet industry standards across various applications.
Anodizing Process Details
The anodizing process of aluminum alloys involves key steps that determine the quality and properties of the surface. Each stage is controlled to achieve the desired mechanical properties. Adjusting parameters like temperature, voltage, and time is crucial for optimizing results based on specific application needs.
Pre-treatment
This initial phase is crucial for preparing the aluminum surface. It includes cleaning, etching, and desmutting. Cleaning removes contaminants like dirt and grease using mild detergents or alkaline solutions. Etching, often done with sodium hydroxide, creates a uniform matte finish by removing surface irregularities. Desmutting follows to eliminate any remaining residues from the etching process, ensuring a clean surface for anodizing.
Anodizing
The core of the process involves immersing the aluminum in an electrolyte bath, typically containing sulfuric or chromic acid. An electric current is applied, causing oxygen ions to form a thick aluminum oxide layer on the surface. This layer is porous, allowing for further treatment like coloring. The process parameters—voltage (usually 15V to 20V), current density (1.0 to 1.5 A/dm²), and time (30 minutes to 2 hours)—are adjusted based on desired thickness and properties of the oxide film.
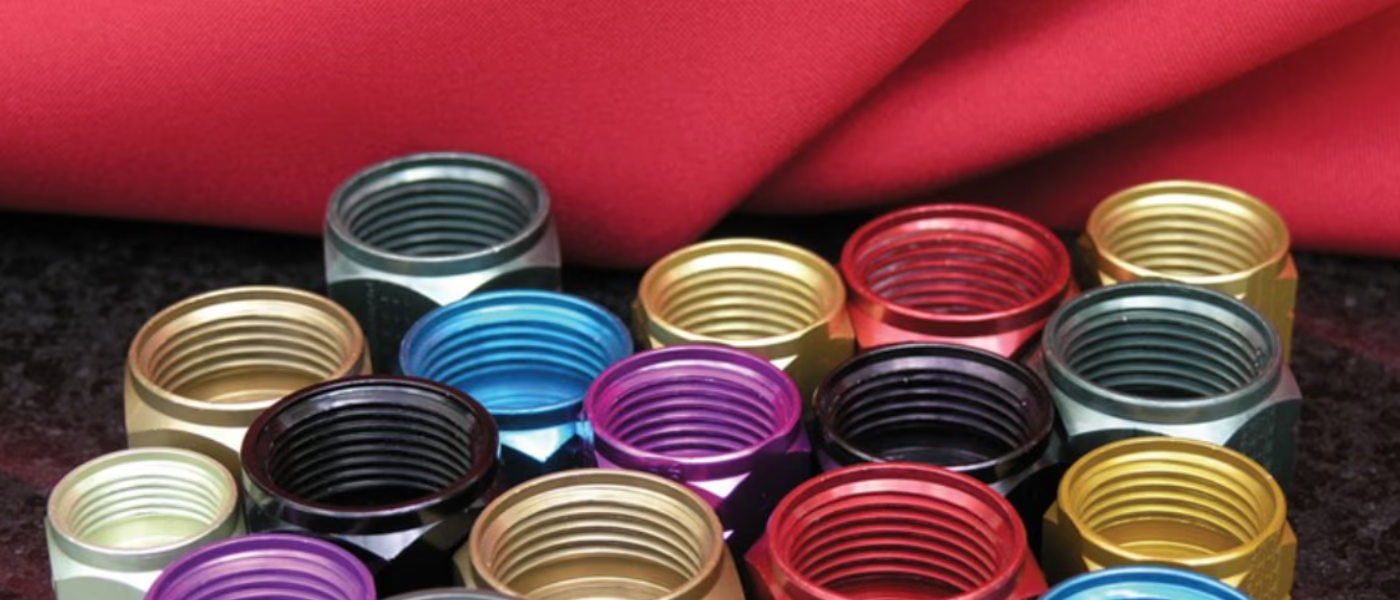
Coloring
If desired, anodized aluminum can be immersed in a dye solution for staining. The porous nature of the oxide layer is permeated and adhered by dye molecules, providing a range of color options. Staining time varies from 10 to 30 minutes, depending on the dye type and concentration.
Sealing
The final step is sealing, which closes the pores of the oxide layer to improve corrosion resistance and durability. This is done using hot water (90°C to 100°C) or steam for 15 to 30 minutes. Proper sealing preserves the anodized surface.
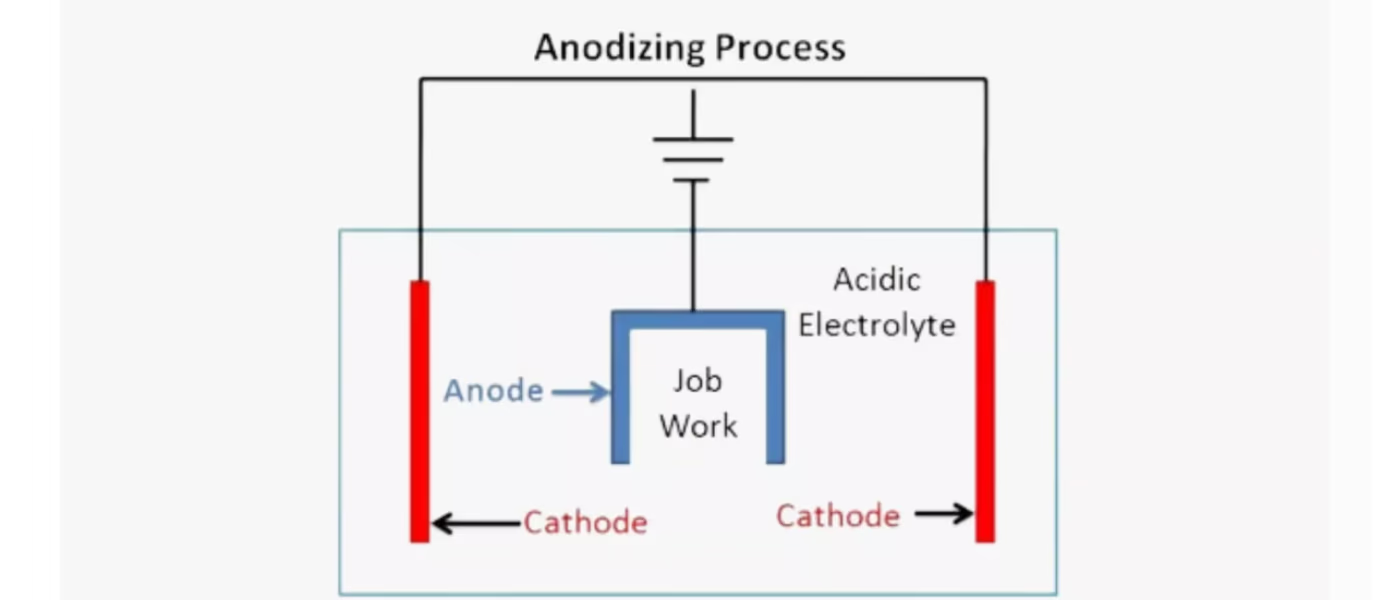
Standards for Different Applications
Aluminium alloy anodizing needs to adhere to specific standards that are tailored to different applications. These standards ensure that anodized coatings meet standards for durability, corrosion resistance, and aesthetics. These standards guide manufacturers in producing high-quality anodized aluminum products that are tailored to the needs of specific industries. By following these guidelines, manufacturers can ensure that their products meet the functionality and aesthetics of a variety of applications.
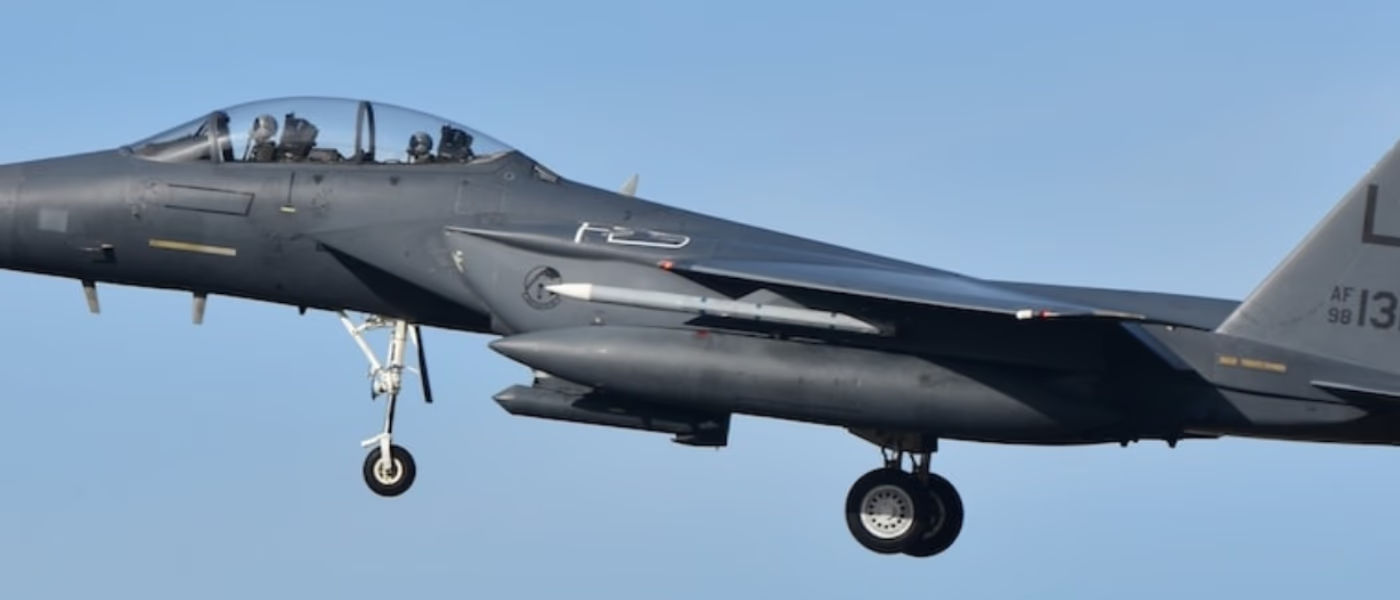
Aerospace Standards
AMS 2472 is a key specification for aerospace applications. It outlines the requirements for anodic coatings that enhance corrosion resistance and surface hardness, which are essential for aerospace components that are exposed to harsh environments for long periods of time. MIL-A-8625 also plays an important role, especially for indirect applications, as it sets the standard for the type and performance of anodizing.
Architectural Standards
AAMA 611 sets the standard for architectural anodized finishes, detailing coating thickness, color uniformity, and corrosion resistance. This standard is essential for applications that require durability in outdoor environments.
Automotive Standards
Specifications such as AMS 2469 and AMS 2482 are commonly used in the automotive industry for anodizing processes. These standards focus on achieving durable finishes that can withstand the harsh environments that cars may encounter, including exposure to weather and road conditions
Challenges in Anodizing Aluminum Alloys
Coloring Defects
Variations in color can occur due to uneven anodizing conditions or improper cleaning. Ensuring uniform cleaning and consistent process parameters like temperature and current density helps mitigate this issue.
Burning and Poor Adhesion
High current densities or insufficient agitation can cause burning on the metal surface, leading to poor adhesion of the oxide layer. Proper monitoring of current settings and ensuring adequate agitation are essential to prevent these defects.
Material Composition
The presence of impurities such as silica in cast aluminum can cause an uneven coating. Due to its porosity and alloying elements, cast aluminum often results in a poor visual appearance.
Electrolyte and Temperature Control
The composition and temperature of the electrolyte bath significantly influence the anodizing process. High temperatures or incorrect acid concentrations can lead to defects like powdering or inadequate film thickness.
Contact Issues
Poor electrical contact between the aluminum parts and the conductor rod can result in partial burns or incomplete anodizing. Ensuring proper contact and adjusting the setup can help avoid these problems
Benefits of Anodized Aluminum
Anodized aluminum offers several advantages that enhance its performance and versatility in a variety of applications: these advantages make anodized aluminum the material of choice for industries ranging from aerospace to consumer electronics.
Enhanced Durability
The anodizing process creates a robust oxide layer on the aluminum surface, significantly increasing its resistance to wear and scratches. This makes anodized aluminum ideal for applications requiring long-lasting materials.
Corrosion Resistance
Anodized aluminum is highly resistant to corrosion because its protective oxide layer protects the metal from environmental factors such as moisture and chemicals. This makes it suitable for environments such as outdoor and marine.
Electrical Insulation
The anodized layer provides excellent electrical insulation, making it useful in electronic components where non-conductive surfaces are required.
Improved Adhesion
The porous nature of the anodized surface allows for better adhesion of paints and adhesives, resulting in more durable finishes and stronger bonds.
Aesthetic Appeal
Anodizing can be used to obtain a vibrant color finish by dyeing, which enhances the aesthetics of aluminum products. This makes it popular in construction and consumer goods applications.
Low Maintenance
Anodized surfaces require little maintenance as they are less susceptible to color and fingerprints. A simple cleaning with water and a soft cloth is usually sufficient.
Environmental Sustainability
The anodizing process is environmentally friendly, producing minimal waste and using non-toxic materials. This makes anodized aluminum a sustainable choice for eco-conscious industries.
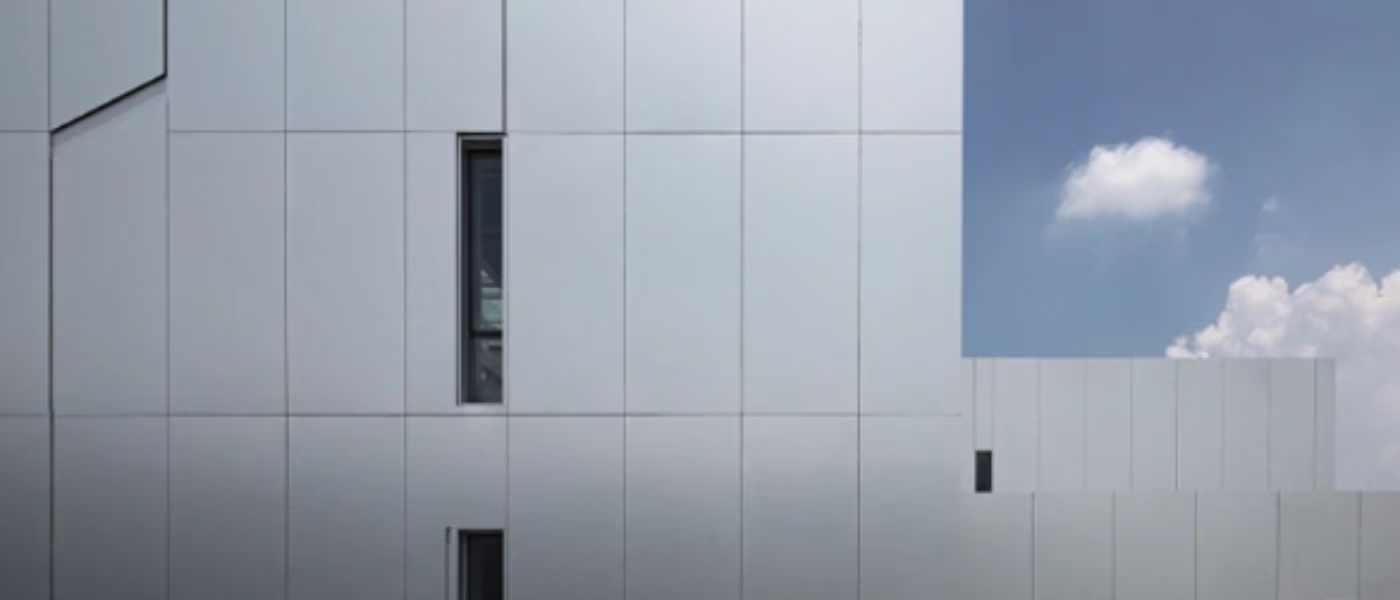
Conclusion
In conclusion, anodizing of aluminum alloys is an important process to improve the durability, corrosion resistance, and aesthetics of materials. By understanding the specifications and standards for anodized aluminum alloys, manufacturers can ensure that the resulting products will deliver consistent quality and performance across a wide range of applications.
Key specifications such as MIL-A-8625, AMS 2472, and ASTM standards provide guidance that can help achieve desired outcomes in different industries, including aerospace, construction, and automotive. The anodizing process involves several key steps – pre-treatment, anodizing, coloring, and sealing – each of which requires precise control to produce a high-quality finish.
Factors such as alloy composition, electrolyte conditions, and process parameters must be carefully managed to avoid issues such as color inconsistencies and poor adhesion. Despite these challenges, the advantages of anodized aluminum are significant. Its enhanced durability, corrosion resistance, and aesthetics make it an option for many applications.
As industries begin to demand materials that combine functionality and sustainability, anodized aluminum remains a valuable option due to its eco-friendly process and long-lasting properties. By adhering to established standards and continuously improving process technology, manufacturers can continue to take advantage of the benefits of anodized aluminum in a variety of applications.
FAQs about Anodizing of Aluminum Alloys
What are the key specifications for anodizing aluminum alloys?
Specifications such as MIL-A-8625 and AMS 2472 provide guidelines on coating thickness, corrosion resistance, and process parameters to ensure high-quality anodized finishes.
How does the anodizing process enhance aluminum alloys?
Anodizing increases corrosion resistance, surface hardness, and allows for color customization, making aluminum alloys more durable and versatile for various applications.
What factors can affect the quality of anodized aluminum?
Factors like alloy composition, electrolyte conditions, temperature, and current density play crucial roles in determining the uniformity and durability of the anodized layer.
What challenges might arise during the anodizing of aluminum alloys?
Challenges include achieving consistent color, managing impurities in the alloy, and ensuring proper electrical contact during the process to avoid defects.
Why is anodized aluminum preferred in certain industries?
Anodized aluminum offers enhanced durability, aesthetic flexibility, and environmental sustainability, making it ideal for aerospace, architectural, and consumer electronics applications.