Water damage accounts for billions in repair costs annually, with inadequate waterproofing being the primary culprit. This guide examines six sheet-applied waterproofing membrane systems used in modern construction and renovation. Each membrane type serves specific purposes—from basic shower protection to specialized steam room applications. Contractors and homeowners alike will find clear comparisons of cost, installation requirements, and performance characteristics. Proper membrane selection is not merely about preventing leaks; it's about protecting your investment for decades to come.

What Are Waterproofing Membranes?
Waterproofing membranes are specialized barrier materials designed to prevent water infiltration into building structures. These engineered systems often comprise multiple layers of materials, each serving a specific function in moisture protection.
Industry professionals typically categorize these protective barriers into sheet-applied and liquid-applied varieties. Sheet membranes come pre-manufactured with consistent thickness (typically 4-8 mil for residential applications), while liquid membranes are applied on-site and cure to form a continuous waterproof surface. Each serves different purposes in construction, with sheet-applied options being particularly suitable for critical wet areas like showers and steam rooms.
Why Waterproofing Is Critical in Wet Areas
Water intrusion in wet areas leads to a predictable sequence of problems. Initial water penetration beyond surface materials causes cosmetic damage, followed by structural issues including warping of wood elements and deterioration of backing materials. EPA studies indicate mold can begin developing within 24-48 hours of water exposure, creating both structural damage and potential health hazards.
The financial implications are significant. Industry data shows that remediation of water damage in a standard bathroom typically costs between 2,500and2,500and10,000—substantially more than the cost of proper initial waterproofing. Cases requiring structural repairs can easily reach five-figure expenses.
Evolution of Waterproofing Technology
Waterproofing has evolved significantly throughout construction history. Ancient Romans used volcanic ash with lime for water-resistant concrete, while Middle Eastern builders applied natural bitumen to waterproof structures.
The early 20th century relied primarily on bituminous products that offered moderate protection but degraded relatively quickly. PVC membranes introduced mid-century represented advancement, though early versions contained plasticizers that leached over time, causing brittleness.
The development of modified polyethylene membranes in the 1980s and 1990s marked significant progress—combining flexibility with durability while maintaining consistent thickness. The integration of non-woven polypropylene fleece created an effective anchoring mechanism for bonding with thin-set mortar.
Recent innovations focus on environmental considerations and performance enhancements, including vapor retardant properties that prevent both liquid water and water vapor migration—especially important in steam environments.
Understanding Sheet-Applied Waterproofing Technology
Sheet-applied waterproofing delivers precision and reliability through pre-manufactured formats. These membranes arrive at construction sites with predetermined thickness, typically 8 mil (0.008 inches) for standard applications or 12 mil for high-movement areas. This consistency ensures uniform protection across the entire installation.
Time efficiency represents another advantage, as sheet membranes can be tiled over immediately after proper installation, unlike liquid membranes requiring curing time before subsequent construction phases.
Composition and Material Science
Modern sheet-applied membranes typically feature a modified polyethylene (PEVA) core, selected for its balance of flexibility and durability. This core provides the primary waterproofing function.
The core is surrounded by non-woven polypropylene fleece on both sides, creating an "anchoring fleece." When embedded in thin-set mortar, these fleece layers create a mechanical bond significantly stronger than simple adhesive connections.
This composition balances competing requirements: flexibility to conform to irregular surfaces, strength to resist installation damage, waterproofing integrity for decades, and minimal thickness to accommodate finished floor heights and wall dimensions.
Vapor Retardant Properties
Beyond stopping liquid water, quality membranes provide vapor retardant properties—crucial in steam environments where water vapor pressure becomes significant.
Water vapor molecules can penetrate materials that block liquid water, potentially condensing within wall cavities and causing hidden damage. High-performance membranes offer vapor retardance ratings (typically below 1.0 perms) that effectively control water in both liquid and vapor states.
Crack-Bridging Capabilities
Effective waterproofing systems must accommodate building movement. Sheet membranes with crack-bridging properties can span minor substrate cracks while maintaining waterproofing integrity, even as buildings settle or experience thermal expansion.
The elasticity of the polyethylene core allows slight stretching rather than tearing when substrate movement occurs. This capability is particularly valuable in renovation projects where existing substrates may have minor imperfections.
VOC Compliance and Environmental Benefits
Leading waterproofing membranes undergo testing against standards like California Specification 01350 for volatile organic compound (VOC) emissions. Low-VOC materials contribute to healthier indoor air quality and often help meet requirements for green building certifications.
Modern sheet membranes typically offer environmental advantages through durability (reducing replacement frequency), compatibility with standard thin-set mortars (eliminating specialized adhesives with potentially harmful chemicals), and effective performance preventing water damage that would otherwise generate construction waste.
Primary Waterproof Membrane for Shower

Sheet-applied polyethylene waterproofing membranes have become the industry standard for shower applications, offering superior performance compared to traditional methods. These specialized membranes address the unique challenges of shower environments—consistent water exposure, temperature fluctuations, and structural movement.
Features and Construction
Modern shower waterproofing membranes feature a layered construction centered around a modified polyethylene core. This 8-mil-thick core provides consistent waterproofing properties throughout the entire installation area. The uniform thickness is critical for reliable performance, eliminating the variability found in field-applied liquid waterproofing products.
The defining characteristic of these membranes is the non-woven polypropylene fleece bonded to both sides of the polyethylene core. This dual-sided fleece creates a mechanical anchoring surface that bonds securely with thin-set mortar. This mechanical bond is substantially more reliable than adhesive-only connections, particularly in environments with regular temperature changes.
Another important feature is the membrane's flexibility, which allows it to conform to various substrate configurations including corners, curves, and transitions between different planes. This flexibility ensures continuous waterproofing coverage even in geometrically complex shower designs.
The 6'7" (2-meter) width available in premium membranes offers significant advantages for wall applications. This dimension allows installation from floor to standard shower head height with minimal seaming, reducing potential failure points and accelerating installation time.
Installation Process
The installation of shower waterproofing membranes follows a methodical process designed to ensure complete water protection:
- Preparation begins with ensuring the substrate is clean, even, and load-bearing—essential for proper membrane adhesion.
- Application requires spreading appropriate thin-set mortar using either a 1/4" × 3/16" V-notched trowel or a specialized 1/8" × 1/8" square-notched trowel. The membrane is pressed firmly into this mortar bed using diagonal sweeps with the flat side of the trowel, eliminating air bubbles that could compromise waterproofing.
- Seaming options include overlapping membrane edges by 2" using unmodified thin-set mortar or abutting edges and covering with a compatible waterproofing strip.
- Corners and transitions require special attention, with pre-formed corner pieces for inside and outside corners and specific waterproofing strips for floor-to-wall connections.
- Pipe protrusions such as showerheads and mixing valves need specialized prefabricated seals with rubber gaskets or appropriate sealant to maintain waterproof integrity.
- Movement joints require accommodation by separating the membrane at existing expansion, structural, and flexible edge joints, then covering with flexible waterproofing strips.
- Water testing should be conducted 24 hours after installation to verify waterproof performance at seams and connections before tile installation proceeds.
Benefits Over Traditional Methods
Compared to traditional shower waterproofing approaches like hot mop or liquid membranes, sheet-applied systems offer several significant advantages:
First, they provide immediate readiness for tile installation without extended curing times. This can reduce overall project timelines by eliminating waiting periods between waterproofing and tile setting.
Second, they maintain consistent thickness throughout the installation area. Unlike liquid-applied products that may be applied unevenly, the factory-controlled thickness ensures uniform protection against water intrusion.
Third, these systems create a complete vapor retardant barrier, protecting the wall cavity from both liquid water and water vapor—particularly important in high-temperature shower environments where steam can penetrate traditional barriers.
Finally, the mechanical bond created by the fleece-reinforced membrane provides superior long-term adhesion compared to systems relying solely on chemical bonds, which can degrade over time due to moisture exposure.
Ideal Applications
These waterproofing membranes perform exceptionally well in several specific applications. Standard residential showers represent the most common usage, where the membrane's efficiency and reliability provide excellent protection for typical daily use.
They're equally effective in bathtub surrounds, providing protection against splash water and occasional spray. The membrane's ability to conform to the irregular junction between tub and wall creates a reliable waterproof seal in this historically problematic area.
For residential steam showers, standard 8-mil membranes provide appropriate protection against both liquid water and limited steam exposure. However, for continuous-use steam rooms or commercial applications, specialized vapor retardant membranes with enhanced performance characteristics may be recommended.
The versatility of these membranes extends to custom shower configurations, including bench seats, niches, and curb-free designs where traditional waterproofing methods often struggle to provide consistent protection across complex geometries.
Waterproofing Strip for Sealing

While the primary waterproofing membrane forms the foundation of a water-tight system, specialized waterproofing strips play a crucial role in creating a complete barrier by addressing specific vulnerable areas.
Purpose and Function
Waterproofing strips serve several essential functions in a comprehensive waterproofing system. Their primary purpose is sealing joints between adjacent sections of waterproofing membrane. These strips create a continuous waterproof barrier across seams, ensuring water cannot penetrate at these potential weak points.
They also provide targeted protection at material transitions, such as the junction between waterproofing membrane and building panels. These transitions create natural discontinuities that require special attention to maintain waterproof integrity.
Additionally, specialized waterproofing strips manage movement at expansion joints. Standard membranes must be separated at these joints to prevent tearing, requiring flexible strips that can accommodate structural movement while maintaining waterproofing.
The strips' 4-mil thickness prevents buildup beneath tile while still providing effective waterproofing. This thin profile allows for smooth transitions without creating noticeable lippage in the finished tile surface.
Installation Techniques
Proper installation of waterproofing strips follows specific techniques to ensure reliability:
For standard seaming between membrane sections, the strips are embedded in the same thin-set mortar used for the primary membrane. They're applied with sufficient overlap (typically 2 inches) onto each adjacent membrane section.
At inside and outside corners, pre-formed corner pieces provide seamless waterproofing around these challenging transitions. These specialty pieces eliminate the need for complex folding or cutting of flat strips, reducing potential failure points.
For expansion joints, flexible waterproofing strips with increased elasticity are installed with the center section tucked into the joint cavity. This configuration allows the strip to stretch and compress with structural movement without compromising waterproof integrity.
When sealing around pipes and fixtures, specialized prefabricated seals with molded rubber gaskets create watertight connections where standard flat strips would be difficult to conform properly.
Critical Areas Requiring Sealing Strips
Several specific areas demand particular attention when waterproofing showers and wet areas:
Floor-to-wall connections represent perhaps the most critical application for waterproofing strips. These 90-degree transitions experience significant water exposure and are prone to movement, making them high-risk areas for water intrusion.
Inside and outside corners present geometric challenges for maintaining continuous waterproofing. The membrane must change direction without creating folds or gaps, requiring specialized corner pieces.
Expansion and movement joints need flexible strips that can accommodate structural movement while maintaining water tightness. Standard membranes would likely tear if installed continuously across these joints.
Pipe protrusions for showerheads, body sprays, and mixing valves create penetrations through the waterproofing plane that require specialized sealing. Prefabricated seals with rubber gaskets ensure water cannot migrate along the pipe penetration.
For curbless shower applications in particular, specialized waterproofing corners for floor/wall/shower base connections require attention, especially when linear drains are installed adjacent to walls.
Integration with Main Waterproofing System
The effectiveness of a waterproofing system depends on proper integration between the primary membrane and sealing components.
All sealing strips must use the same bonding materials as the main membrane—typically unmodified thin-set mortar—to ensure compatible adhesion and similar aging characteristics over time.
Overlaps between strips and the main membrane should maintain consistent minimum dimensions (typically 2 inches) to create reliable waterproof seams. Insufficient overlap can create vulnerable transition points.
For connections to fixed building elements, appropriate sealing compounds complement the waterproofing strips. These may include specialized sealants designed to work with the membrane system or trowel-applied waterproofing materials that cure with atmospheric moisture.
In specialized applications like curbless showers, the integration between floor waterproofing, wall membranes, and linear drain flanges requires careful coordination of compatible components designed to work as a system.
The entire assembly—primary membrane plus all seaming and sealing components—should be viewed as an integrated system rather than individual parts. When properly executed, this comprehensive approach creates a truly waterproof enclosure that will protect the building structure for decades.
Mixing Valve Seal Waterproofing Membrane
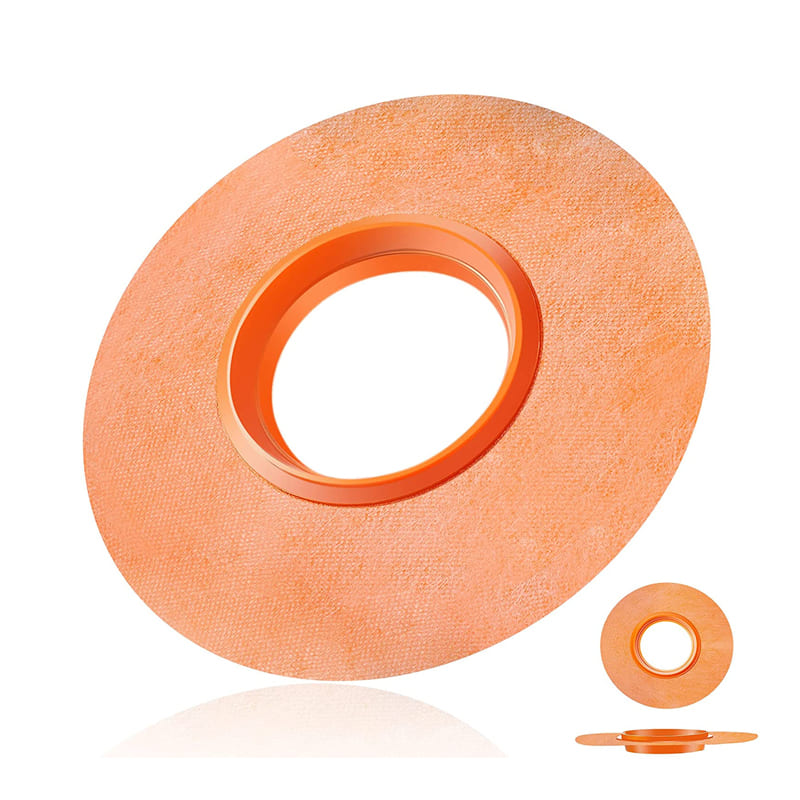
Shower mixing valves represent a significant vulnerability in any waterproofing system. These control mechanisms typically require a large opening in the waterproofing plane, creating potential for water intrusion into wall cavities.
Protection for Plumbing Installations
Mixing valve seals consist of prefabricated waterproofing sections with over-molded rubber gaskets designed specifically for these irregular openings. The rubber gasket forms a precise opening that conforms to standard mixing valve configurations while the surrounding waterproofing material membrane system.
The 4-mil thickness of these specialized seals maintains consistency with the primary waterproofing system while providing adequate strength at this critical juncture. This measured thickness prevents unwanted buildup at the valve location that could affect finished wall dimensions.
Field research from remediation specialists shows that up to 17% of shower leaks occur at mixing valve locations, underscoring the necessity for proper sealing in this area. The modest cost of specialized seals becomes insignificant when compared to potential repair expenses.
Installation Around Plumbing Fixtures
Installing mixing valve seals requires coordination with plumbing rough-in work:
- The mixing valve must be properly secured to blocking within the wall assembly before waterproofing begins.
- The prefabricated seal is applied after the primary waterproofing membrane, creating an overlapping connection that directs water away from the valve opening.
- The rubber gasket portion must fit snugly against the valve body to prevent water migration between these components.
- Thin-set mortar bonds the waterproofing portion to the surrounding membrane using the same technique as other seaming operations.
Preventing Water Damage at Critical Control Points
Mixing valves control temperature and flow—functions that require mechanical components behind the finished wall surface. The electronic components in modern thermostatic mixing valves are particularly vulnerable to moisture damage.
The seal protects exposed edges of moisture-sensitive backing panels at the valve opening. Without this protection, water can wick into these materials, causing deterioration over time.
The rubber gasket component compensates for irregularities in the valve mounting, creating a reliable seal even when the valve isn't perfectly aligned with the wall surface.
Common Installation Challenges
Several common issues can compromise mixing valve seal performance:
Improper sizing occurs when the seal doesn't match the specific valve configuration. Most manufacturers offer multiple dimensions to accommodate various valve designs.
Misalignment happens when the valve body isn't parallel to the wall surface. While the rubber gasket provides some flexibility, extreme angles may prevent proper sealing.
Insufficient bonding between the seal and surrounding waterproofing membrane often results from inadequate thin-set mortar application or premature disturbance during installation.
Multiple penetrations for separate volume controls or diverters require careful planning to maintain waterproof integrity between closely spaced openings.
Waterproofing Collar for Pipe Seal
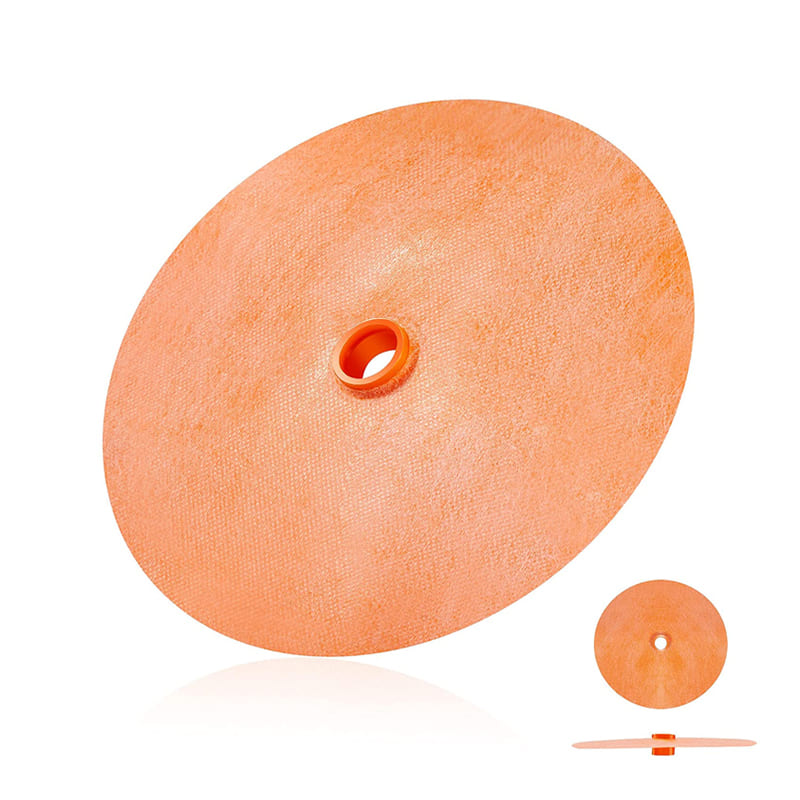
Pipe penetrations present unique waterproofing challenges due to their circular shape and the need for a perfect seal against a smooth surface.
Addressing Pipe Protrusions
Pipe seal collars utilize similar technology to mixing valve seals—prefabricated waterproofing material with molded rubber gaskets designed for specific pipe diameters. The rubber portion creates a tight seal against the pipe while the surrounding waterproofing material bonds with the primary membrane.
These seals accommodate pipes for showerheads, body sprays, tub spouts, and other necessary penetrations. Most manufacturers offer various sizes to match standard plumbing pipe diameters (½", ¾", 1").
Testing shows that properly installed pipe seals maintain watertight performance even with water pressure applied directly at the penetration point. This resilience comes from the combination of the flexible rubber gasket and the mechanical bond of the waterproofing material.
Integration with Main Waterproofing System
The integration between pipe seals and the primary waterproofing membrane follows a specific sequence:
- The primary membrane is installed first across the general wall area.
- Pipe penetrations are identified and appropriate sized seals are selected.
- The pipe seal is applied over the primary membrane with sufficient overlap (typically 2 inches minimum).
- The same thin-set mortar used for the primary membrane bonds the pipe seal, creating material consistency throughout the system.
This layered approach creates a shingle effect where water flows down the wall and over connections rather than against them, reducing the potential for intrusion.
Installation Best Practices
Proper installation of pipe seals requires attention to several details:
Pipes must be clean and free of oils, dust, or debris that could prevent the rubber gasket from sealing properly.
Placement should center the pipe in the gasket opening without stretching or compressing the rubber component. Distortion of the gasket shape can compromise the watertight seal.
For shower applications with removable shower arms, the seal must be installed against the permanent pipe nipple rather than the removable component.
Temperature considerations are important during installation. Extreme cold can make rubber gaskets less flexible, while excessive heat may cause unwanted expansion. Installation at moderate temperatures (60-80°F) provides optimal results.
Additional Sealant Requirements
In certain situations, supplementary sealants may be necessary:
Alternative waterproof sealing methods may be used when standard pipe seals don't match unusual pipe sizes. Specialized sealants compatible with both the pipe material and the waterproofing membrane can create custom solutions.
For threaded connections that may experience slight movement during fixture installation, a small amount of supplemental sealant provides additional protection.
When pipes penetrate moisture-sensitive backing panels in areas not covered by the prefabricated seal, appropriate sealant should protect these vulnerable materials.
For steam shower applications with higher vapor pressure, additional vapor-resistant sealant may be recommended around pipe penetrations to ensure complete protection against both liquid water and water vapor.
Proper material selection is critical, as some sealants contain solvents that could potentially damage certain waterproofing membranes or pipe materials. Always verify compatibility between components before application.
Inside Corners Waterproofing Membrane
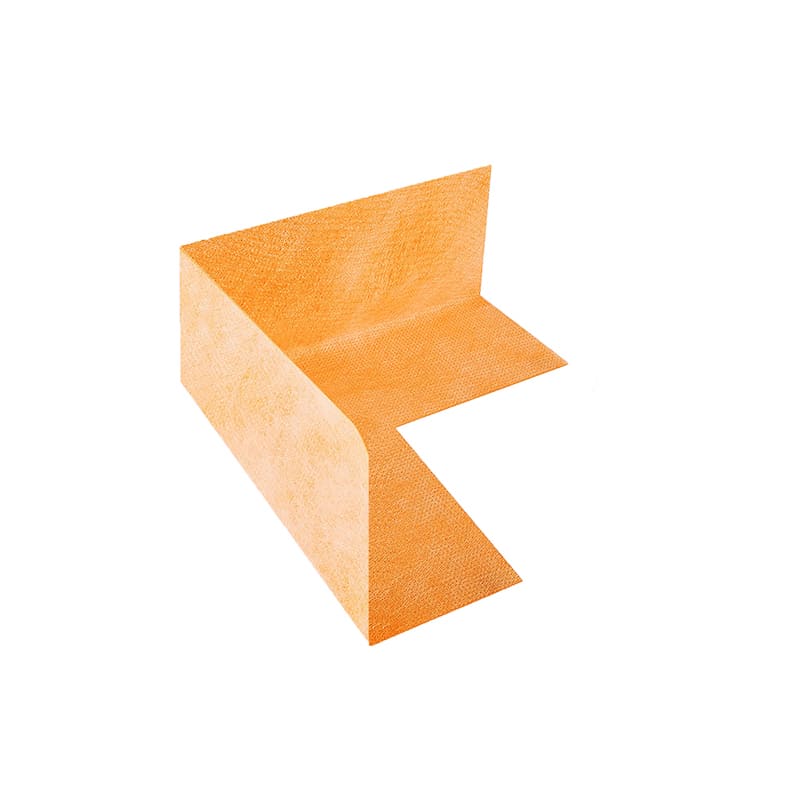
Inside corners represent critical junctions in waterproofing systems where wall planes meet each other or floors. These 90-degree transitions create natural stress points where waterproofing continuity becomes particularly challenging.
Design Considerations
Preformed inside corner pieces eliminate the need for complex folding or cutting of flat waterproofing membrane. These purpose-made components provide consistent thickness throughout the corner transition—typically maintaining the same 4-mil thickness as the primary membrane.
The geometrical configuration of inside corners creates natural collection points for water in shower applications. Water naturally flows downward along walls and concentrates at these junctions, making proper sealing here particularly crucial.
The dimensional stability of preformed corners outperforms field-fabricated solutions. Manufacturing processes create precisely formed angles that maintain their shape during installation, unlike field-cut membrane pieces that may distort when manipulated.
Installation Best Practices
Installation of inside corner waterproofing follows a methodical approach:
- The primary waterproofing membrane is installed on adjacent wall surfaces, leaving the corner junction open.
- Thin-set mortar is applied to the corner area using the appropriate notched trowel (typically 1/8" × 1/8" square-notched).
- The preformed corner piece is pressed into position, ensuring complete contact with the thin-set mortar beneath.
- Using the flat side of the trowel, the installer applies firm pressure to embed the corner piece, working from the center outward to eliminate air pockets.
- The edges of the corner piece must overlap the primary membrane by at least 2 inches to create a continuous waterproof barrier.
Waterproofing Integrity at Corner Transitions
The corner transition presents unique waterproofing challenges that preformed pieces address effectively. The consistent thickness at the corner eliminates the problematic double or triple thickness that occurs when folding flat membrane sections.
The seamless construction of preformed corners eliminates potential leak paths that might develop at cut edges or folds when using standard membrane pieces. This single-piece approach creates continuous protection throughout the critical corner zone.
Proper bonding at corners requires complete contact between the preformed piece and the substrate. The specialized fleece backing on these corners creates the same mechanical bond with thin-set mortar as the primary membrane, ensuring consistent adhesion characteristics throughout the system.
Preventing Moisture Penetration at Vulnerable Points
Several specific inside corner configurations require particular attention:
Floor-to-wall junctions represent perhaps the most critical application for inside corner waterproofing. These areas experience significant water exposure and are prone to structural movement, creating high-risk conditions for water intrusion.
Shower bench-to-wall connections create complex geometries where standard waterproofing approaches often fail. Preformed corners designed specifically for these transitions maintain waterproof integrity without creating excessive buildup.
For shower niches, specialized inside corners properly seal the six internal corners typical in these installations. The concentrated waterproofing in these decorative yet functional spaces prevents moisture damage to the surrounding wall cavity.
In neo-angle shower designs, specialized inside corner pieces may be required for the 135° angles formed where walls meet. Standard 90° corners cannot properly waterproof these non-standard angles without modification.
Outside Corners Waterproofing Membrane
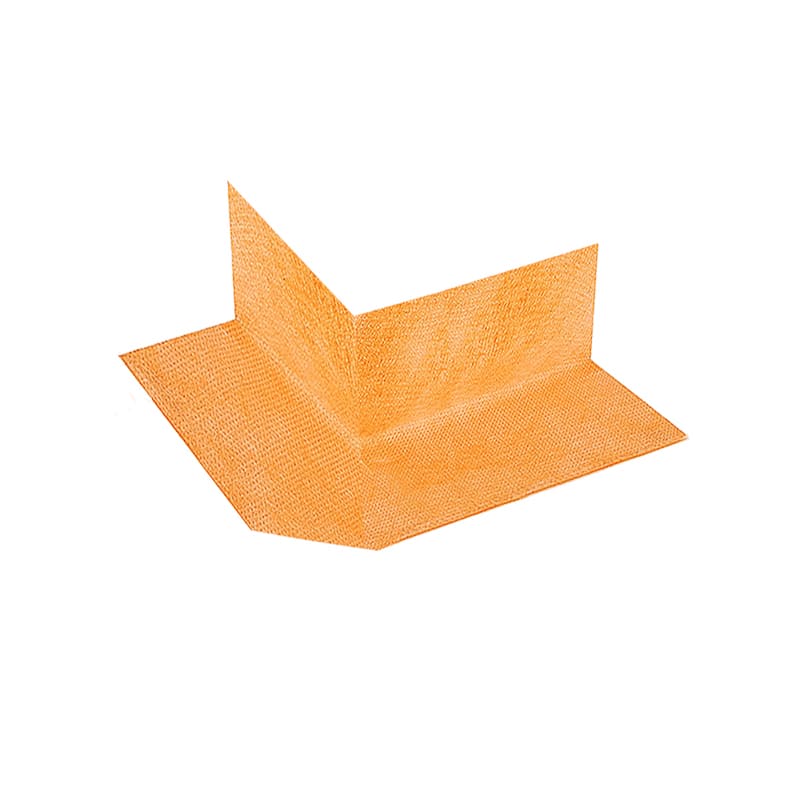
Outside corners present distinct waterproofing challenges compared to inside corners. These projecting edges are exposed to physical impact and create complex geometric transitions that standard membranes cannot easily navigate.
Preventing Leaks at Vulnerable Points
Preformed outside corner pieces solve several key waterproofing challenges. Their molded construction eliminates the need to cut and fold flat membrane material, which can create weak points and inconsistent coverage at these critical junctions.
The physical vulnerability of outside corners makes proper waterproofing particularly important. These projecting edges experience more physical contact during construction and use, increasing the risk of membrane damage compared to protected inside corners.
Outside corners on shower curbs, bench edges, and half-walls create natural termination points for tile installations. Proper waterproofing at these locations prevents water from migrating behind finished surfaces at these transitions.
Seamless Integration Techniques
Installing outside corner waterproofing requires specific techniques:
- The primary waterproofing membrane is applied to adjacent wall surfaces, stopping short of the outside corner edge.
- Appropriate thin-set mortar is applied to the corner area using the recommended notched trowel pattern.
- The preformed outside corner is positioned over the corner and pressed firmly into the mortar bed.
- Using the flat side of the trowel, pressure is applied from the corner apex outward to eliminate air pockets and ensure complete bonding.
- The edges of the preformed piece must overlap the main membrane by the manufacturer's recommended distance (typically 2 inches) to create a continuous waterproof plane.
Maintaining Consistent Membrane Thickness
One of the primary advantages of preformed outside corners is thickness consistency. These factory-formed pieces maintain uniform 4-mil thickness throughout the corner transition, avoiding the problematic buildup that occurs when folding standard membrane.
This consistent thickness prevents unwanted protrusions in the finished tile surface. When standard membrane is folded to create outside corners, the doubled or tripled thickness can create noticeable lippage in thin-set tile installations.
The manufacturing process for preformed corners ensures geometrical accuracy that field-fabricated solutions cannot match. This precision creates reliable waterproofing while maintaining the proper substrate profile for tile installation.
Special Installation Considerations
Different outside corner applications present unique challenges:
Shower curb corners experience significant water exposure and physical stress. Proper installation here requires complete coverage of the curb's three exposed surfaces (top and both sides) with appropriate overlap onto adjacent waterproofing.
Shower bench front edges need protection without creating excessive buildup that might affect the finished tile profile. Preformed corners designed specifically for benches address the particular geometry of these features.
Window sills within shower enclosures require special attention to prevent water infiltration into the wall cavity below. Preformed outside corners properly seal these vulnerable transitions when standard membrane cannot easily conform to the complex geometry.
For non-standard angles, such as those found in custom shower designs, specialized corner pieces may be required. Standard 90° corners cannot properly waterproof acute or obtuse angles without modification or custom fabrication.
Installation Best Practices
Proper installation of waterproofing membranes determines their effectiveness regardless of material quality. Research by the Tile Council of North America indicates that over 70% of shower waterproofing failures stem from installation errors rather than material defects.
Surface Preparation Requirements
Surface preparation fundamentally affects membrane adhesion and performance:
The substrate must be structurally sound with no significant deflection. Industry standards typically limit deflection to L/360 under full load (where L represents the span length in inches). Excessive deflection creates stress points in the membrane that can lead to failure over time.
Surfaces must be clean and free of contaminants. Dust, oils, and residues create bond barriers between the membrane and substrate. Vacuum cleaning followed by wipe-down with appropriate cleaners ensures proper adhesion.
Substrate moisture content must fall within acceptable parameters. Cementitious substrates should generally measure less than 4% moisture content before membrane application. Excessive substrate moisture can inhibit proper curing of adhesives and compromise long-term performance.
Surface temperature affects adhesion quality. Most systems require substrate temperatures between 50°F and 90°F (10°C-32°C) for optimal bonding. Applications outside this range can impair mortar hydration and proper membrane attachment.
Surface flatness tolerances are critical for proper membrane installation. Industry standards typically specify maximum variation of ¼ inch in 10 feet for floors and ⅛ inch in 8 feet for walls when measured with a straightedge. Excessive variation can create voids beneath the membrane or stretching that compromises waterproofing integrity.
Adhesion Techniques
Proper adhesion techniques ensure complete membrane bonding to the substrate:
Trowel selection directly impacts adhesive coverage. For most sheet membranes, a ¼" × 3/16" V-notched trowel or 1/8" × 1/8" square-notched trowel provides optimal mortar distribution. Using the wrong trowel size can result in insufficient mortar for proper embedding or excessive mortar that creates uneven thickness.
Mortar open time (the period when mortar maintains adhesive properties) must be observed. This typically ranges from 15-30 minutes depending on environmental conditions. Working beyond the open time results in poor adhesion as the mortar forms a surface skin that prevents proper bonding.
Embedding technique significantly affects membrane adhesion. After placing the membrane in fresh mortar, applying pressure with the flat side of the trowel in diagonal sweeping motions ensures complete contact and eliminates air pockets. This technique resembles wallpaper installation rather than tile setting.
Mortar coverage beneath the membrane should reach 100% for proper waterproofing. Unlike tile installation where 80% coverage might be acceptable, waterproofing membranes require complete support to function properly. Voids beneath the membrane become potential leak paths over time.
Temperature and humidity affect working time and curing rates. In hot, dry conditions, mortar may dry too quickly, while cold, humid conditions extend curing time. Adjusting work pace to match environmental conditions ensures proper membrane bonding.
Seaming Methods
Seam construction represents a critical aspect of membrane installation:
Overlap dimensions must meet manufacturer specifications, typically 2 inches minimum. This overlap creates a shingle effect where water flows over rather than against the seam, reducing potential for water intrusion. Insufficient overlap creates vulnerability at these transitions.
Seam bonding requires the same thin-set mortar used for membrane attachment. The consistency of materials throughout the system ensures compatible cure rates and long-term performance. Applying a continuous layer of mortar within the full overlap area prevents potential leak paths.
Overlap direction should consider water flow patterns. Vertical seams should be constructed so the upper section overlaps the lower section, creating a shingle effect that directs water away from rather than into the seam.
Air entrapment within seams must be eliminated. Air pockets create potential leak paths and weak points in the waterproofing system. Careful smoothing with the flat edge of the trowel removes air and ensures complete contact between overlapped membrane sections.
Alternative seaming methods may involve butting membrane edges and covering the joint with specialized waterproofing tape. This approach maintains consistent membrane thickness throughout the installation, which can be advantageous for certain applications like steam showers.
Curing and Testing
Post-installation procedures ensure system integrity before covering with finished materials:
Initial cure time before flood testing typically ranges from 24 to 72 hours, depending on environmental conditions and system specifications. Premature testing can damage partially cured seams and connections.
Flood testing protocols generally specify maintaining 2 inches of standing water for a minimum of 24 hours. Marking the water level at the start of the test period allows for detection of even slight water loss that might indicate a leak.
Documentation of testing provides liability protection and quality assurance. Photographs showing proper water depth at the beginning and end of the test period, along with written records of test duration and results, create a valuable installation record.
Drain plugs used during testing must create complete seals without damaging the waterproofing membrane. Mechanical test plugs installed from above are preferred over plugs inserted into the drain pipe from below, which can damage membranes that extend into the drain.
Visual inspection of vulnerable points should accompany flood testing. Even with successful water retention, careful examination of seams, corners, and penetrations may reveal potential issues that could develop into problems over time.
Troubleshooting Common Waterproofing Challenges
Even with proper installation, waterproofing systems may develop issues that require troubleshooting and remediation. Understanding common failure modes aids in prevention and repair.
Identifying Potential Failure Points
Several key indicators help identify developing waterproofing issues:
Efflorescence (white mineral deposits) on finished surfaces often indicates water migration through building materials. While not always directly related to waterproofing failure, efflorescence suggests moisture movement that warrants investigation.
Grout deterioration, particularly along floor-wall junctions, frequently signals water intrusion beneath the tile. The dissolution of cementitious materials creates visible erosion patterns as water moves through these areas.
Mildew or mold growth on finished surfaces, especially in patterns that don't correlate with normal water exposure, suggests moisture behind these materials. Such growth often appears first in corners or along seams where waterproofing may have failed.
Hollow-sounding tiles detected by tapping may indicate moisture-compromised setting materials beneath. Water intrusion often causes thin-set mortar deterioration, creating detectable voids beneath affected tiles.
Visible substrate swelling or discoloration in adjacent areas (like ceilings below or walls adjacent to wet areas) provides clear evidence of water migration beyond the waterproofed zone.
Repairing Damaged Membranes
Remediation approaches depend on damage extent and accessibility:
For accessible membrane damage prior to covering installation, patch repairs can be effective. These involve cleaning the damaged area, applying new membrane material with appropriate overlap (minimum 2 inches beyond damage in all directions), and ensuring proper bonding with compatible thin-set mortar.
When damage occurs during fixture installation, specialized sealants compatible with the membrane material can repair punctures or tears. These elastomeric sealants bond to the membrane while maintaining waterproof properties.
For significant or inaccessible damage, section replacement may be necessary. This involves removing finished materials to access the damaged area, replacing the affected membrane section with proper overlaps onto sound material, and reinstalling finished surfaces.
Steam shower membrane failures require particularly thorough remediation due to the high moisture levels involved. Simply patching visible damage may not address underlying issues, as steam penetration often extends beyond obvious damage points.
Root cause analysis should accompany all repairs to prevent recurrence. Understanding whether damage resulted from installation errors, mechanical impact, material failure, or substrate movement helps determine appropriate repair strategies.
Quality Control Measures
Preventive measures significantly reduce waterproofing failures:
Installer certification ensures proper training in system-specific installation techniques. Manufacturers often offer training programs that cover their particular products and methods, reducing installation errors.
Independent inspection at critical installation phases provides objective quality verification. Having knowledgeable third-party inspectors examine substrate preparation, membrane application, and seaming before covering installation can identify issues while remediation remains relatively simple.
Photographic documentation creates valuable records of properly completed waterproofing. Images showing correct membrane overlaps, corner treatments, and penetration seals provide reference for future troubleshooting if needed.
Material compatibility testing prevents adverse interactions between system components. When using products from different manufacturers, verify compatibility through manufacturer documentation or small-scale testing before full installation.
Maintenance education helps property owners identify early warning signs of waterproofing issues. Simple guidance about monitoring grout condition, watching for unusual staining, and periodic seal inspection can prevent minor problems from developing into major failures.
Applications Beyond Showers
While shower enclosures represent the most common application for sheet-applied waterproofing membranes, these versatile materials provide effective moisture protection in numerous other settings. The same properties that make them ideal for showers—reliability, ease of installation, and compatibility with tile finishes—translate well to other moisture-challenged environments.
Bathtub Surrounds
Bathtub surrounds benefit from sheet-applied waterproofing in several key ways:
Unlike showers, bathtubs themselves provide the primary waterproofing for the floor area, with the membrane only needed on surrounding walls. The tub handles floor waterproofing while the membrane protects the walls.
Installation requires special attention at the tub-to-wall transition. The membrane must extend down over the tub flange by at least 1/4 inch, creating a waterproof overlap that prevents moisture intrusion behind the tub.
For bathtub surrounds, the waterproofing membrane typically needs to extend only to a height of 3 inches above the shower head or around 6 feet minimum. This strategic protection focuses on the splash zone where water exposure actually occurs.
Freestanding tubs present a different challenge. Without a wall flange, waterproofing strategies focus on floor protection against splash and overflow, essentially creating a protected zone extending about 12 inches beyond the actual tub perimeter.
Steam Rooms
Steam rooms create uniquely demanding conditions for waterproofing systems:
Unlike standard showers, steam rooms expose waterproofing to continuous high-temperature moisture in vapor form. The exposure pattern differs significantly from intermittent liquid water contact.
Specialized vapor-retardant membranes provide significantly lower vapor permeance (typically under 0.5 perms) compared to standard shower membranes. This enhanced vapor-blocking capability is essential for preventing moisture migration through walls and ceilings.
Complete room coverage is essential in steam applications. Whereas standard shower waterproofing might stop at 3 inches above the showerhead, steam room applications require membrane installation on all surfaces including walls and ceiling, creating a complete moisture envelope.
Seaming requires particular attention in steam environments. The increased pressure from steam can force moisture through even minor imperfections in seams that might perform adequately in standard shower applications.
Material compatibility with high temperatures must be considered. Some sealants and adhesives that perform well in normal shower temperatures may degrade under the sustained heat of steam rooms (typically 110-120°F).
Commercial Wet Areas
Commercial applications present unique waterproofing challenges and requirements:
Higher use frequency intensifies exposure patterns. A residential shower might see 15 minutes of use daily, while commercial facilities can experience nearly continuous operation.
Code compliance often differs for commercial applications, with more stringent requirements for waterproofing continuity and performance testing. Commercial projects frequently require compliance with additional standards like ANSI A118.10 for waterproofing membranes.
Large-scale installations create more seams and transitions that require careful waterproofing. While a home shower might have 8-12 linear feet of corners to waterproof, commercial locker rooms can have hundreds, creating exponentially more potential failure points.
Integration with floor drainage systems differs in commercial settings. Rather than single-point drains common in residential applications, commercial wet areas often utilize linear drains or multiple drainage points, creating additional penetrations requiring proper waterproofing.
Maintenance access may need to be incorporated into the waterproofing design. Commercial facilities often require periodic access to plumbing or mechanical systems, necessitating removable panels or access points that maintain waterproofing integrity while allowing future maintenance.
Exterior Applications
Exterior waterproofing applications introduce additional variables beyond those encountered in interior settings:
Temperature cycling creates expansion and contraction stresses that interior applications rarely experience. Exterior waterproofing must accommodate this movement through flexible membranes and properly designed movement joints.
UV exposure can degrade some waterproofing materials over time. Products suitable for exterior applications incorporate UV stabilizers or require protective coverings to prevent deterioration.
Freeze-thaw cycles in cold climates create additional stresses. Water that penetrates tiny cracks can expand when frozen, enlarging these openings and compromising waterproofing over time.
Exterior applications often require integration with additional building envelope components such as flashings, weeps, and air barriers. This creates a more complex waterproofing system with multiple materials that must work together harmoniously.
Drainage considerations become more critical in exterior applications. While interior waterproofing primarily prevents water penetration, exterior systems must both block water and direct it away from the structure.
Choosing the Right Waterproofing System
Selecting the appropriate waterproofing approach requires balancing multiple factors including intended use, substrate conditions, installation timeframe, and budget constraints.
Project Assessment Factors
Thorough project evaluation improves waterproofing outcomes:
Use pattern intensity directly impacts system selection. A master bathroom used daily by two people presents different requirements than a hotel shower used by hundreds of guests monthly.
Substrate type significantly influences system compatibility. Cement board, fiber cement board, gypsum boards, concrete, and plywood each present different bonding characteristics and movement potentials. The waterproofing system must accommodate these specific properties.
Project timeline considerations may limit options. Some systems require longer curing periods before flood testing or tile installation can begin. When scheduling is tight, rapid-setting systems may justify higher material costs by reducing overall project duration.
Environmental conditions during installation affect system selection. Projects in high-humidity environments or extreme temperatures may require specialized materials or installation techniques.
Structural movement expectations influence system choice. Buildings with significant deflection or settlement potential require more flexible waterproofing systems to accommodate movement without compromising integrity.
Material Compatibility Considerations
The interaction between waterproofing and adjacent materials determines long-term performance:
Setting materials must be compatible with the chosen waterproofing system. Some membranes require specific thin-set mortars for proper bonding both beneath the membrane and for tile installation.
Sealant compatibility requires verification, particularly at movement joints and penetrations. Incompatible sealants may fail to bond properly or can chemically degrade the waterproofing membrane.
Drain assemblies must integrate properly with the waterproofing system. Membranes typically require specific drain types with appropriate bonding flanges to create a watertight seal.
Building panel selection affects waterproofing performance. Some panels provide inherent water resistance that complements the primary waterproofing, while others may deteriorate if moisture penetrates the membrane.
Metal components in contact with waterproofing require attention to prevent galvanic corrosion. Stainless steel fasteners and accessories generally perform better than standard steel or aluminum in wet environments.
Cost vs. Long-Term Performance
Economic considerations must balance initial expenses against long-term outcomes:
Material costs represent only a fraction of overall waterproofing expenses. Lower-priced materials that require more complex installation may ultimately cost more than premium products with simpler application methods.
Installation efficiency varies significantly between systems. Sheet-applied membranes typically install faster than multiple-coat liquid applications, potentially offsetting higher material costs through labor savings.
Remediation expenses for failed waterproofing far exceed proper initial installation costs. When waterproofing fails, repair typically involves removing and replacing finished surfaces, addressing substrate damage, and reinstalling the entire system.
System warranty value varies widely between products. Some manufacturers offer limited material warranties while others provide comprehensive coverage including replacement labor. This significant difference can impact long-term value.
Life-cycle analysis often favors higher-performance systems despite greater initial costs. When installation, maintenance, expected lifespan, and potential replacement costs are considered together, premium waterproofing systems frequently demonstrate superior long-term value.
Conclusion: Future of Waterproofing Technology
Sheet-applied waterproofing membranes have revolutionized moisture protection in wet areas, offering reliable performance when properly selected and installed. For professionals and DIYers alike, understanding the key differences between available systems is essential for project success.
Membrane Type | Best Applications | Key Advantages | Considerations |
---|---|---|---|
Standard Sheet Membrane | Showers, tub surrounds | Easy installation, consistent thickness | Requires careful seaming |
Vapor-Retardant Membrane | Steam rooms, saunas | Superior vapor blocking (<0.5 perms) | Higher cost, specialized installation |
Liquid-Applied Membrane | Complex geometries, retrofits | Seamless coverage, conforms to irregular surfaces | Thickness control challenges, longer curing time |
Composite Membrane | High-movement areas | Enhanced crack-bridging capability | Typically thicker, may require adjustment at transitions |
Self-Adhered Membrane | Quick installations, repairs | Eliminates separate adhesive application | Temperature sensitivity during installation |
Fleece-Lined Membrane | Concrete substrates, uncured installations | Excellent bonding in challenging conditions | Requires specific setting materials |
Looking forward, waterproofing technology continues to evolve with several promising developments. Next-generation membranes will likely incorporate enhanced vapor management capabilities, improved flexibility to accommodate structural movement, and simplified installation methods to reduce labor costs and potential errors. Smart waterproofing systems with embedded sensors may soon allow for real-time moisture monitoring and early leak detection before damage occurs.
The most significant advancement may come from systems that combine waterproofing with additional functionalities such as thermal insulation, sound attenuation, and crack isolation—creating truly multifunctional building envelope solutions. As building science continues to advance, these integrated approaches will help create more resilient, efficient, and durable structures for both residential and commercial applications.