Have you ever wondered how magnificent structures like skyscrapers and bridges withstand the test of time, weather, and natural disasters? The secret lies not just in the materials used but in the ingenious integration of movement and expansion joints within these structures.
Dive into the fascinating world of construction technology with us and learn what is a movement joint in construction.
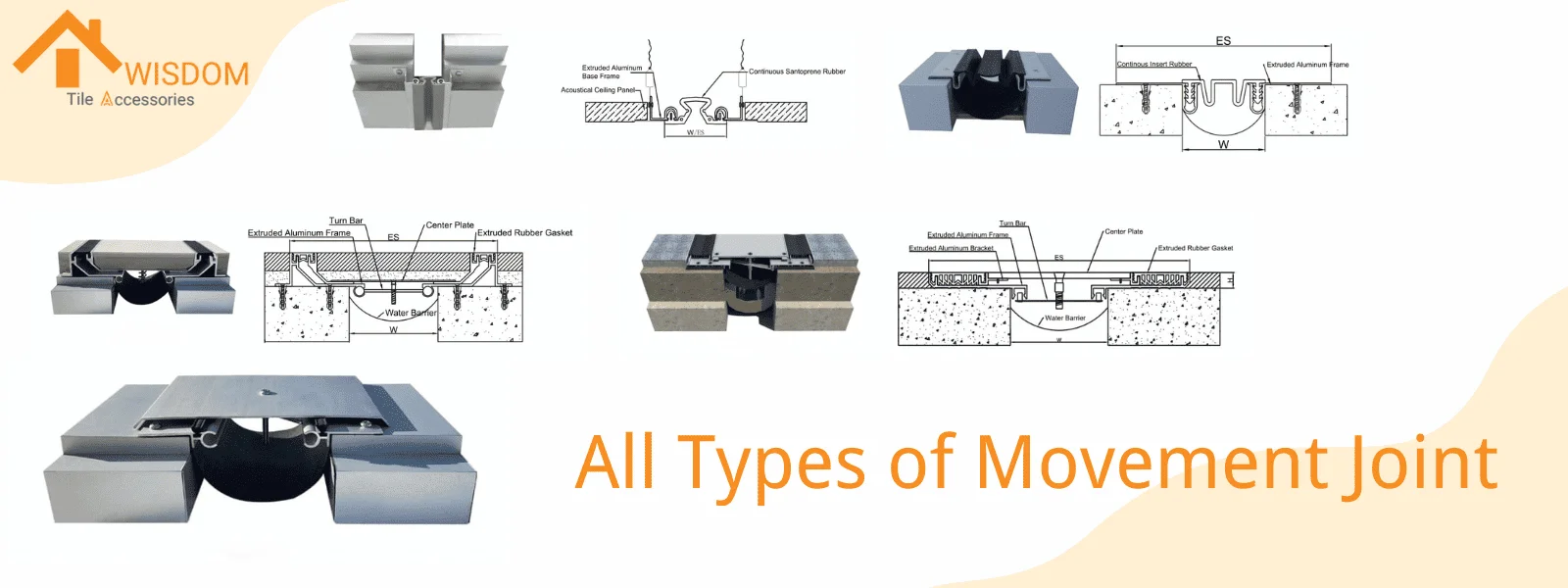
What is a Movement Joint?
A movement joint, often referred to as an expansion joint within the context of construction and engineering, is a deliberate interruption in the continuity of a structure designed to absorb and accommodate the expansion and contraction movements caused by temperature variations, shrinkage, or seismic activities, without inducing stress into the building components. These joints are integral to the longevity and durability of a structure, ensuring that natural movements do not lead to damage or failure of the building materials. By allowing for controlled movement, these joints help maintain the structural integrity and functionality of buildings and infrastructure over time.
What does a Movement Joint do?
The primary function of a movement joint is to allow for the safe and predictable expansion and contraction of construction materials, which can be induced by thermal changes, moisture variation, creep, or load changes. This capability is crucial for preventing cracks and other structural damages that can occur when different parts of a building expand or contract at different rates. Movement joints are strategically placed in buildings, bridges, roads, and other structures to ensure that they can adapt to environmental and load-induced stresses without causing harm to the structure itself.
They play a critical role in:
- Mitigating Stress: By absorbing the expansion and contraction of materials, movement joints reduce the stress that can lead to structural damage.
- Enhancing Durability: They contribute to the longevity of a structure by preventing cracks and separations that can compromise its integrity.
- Improving Safety: By maintaining the structural integrity, movement joints indirectly contribute to the safety of the occupants and users of the structure.
- Accommodating Movement: In areas prone to seismic activity, movement joints allow structures to flex and move with the ground motion, reducing the risk of catastrophic failure.
Main Types of Movement Joint
Movement Control Joint
Movement control joints are specialized architectural features designed to mitigate the effects of localized compression and expansion stresses within structural components. These joints are engineered to be minimally visible, blending seamlessly into the environment often resembling a groutline. They play a critical role in maintaining the integrity and longevity of tiled surfaces by accommodating the natural movements of the building materials.
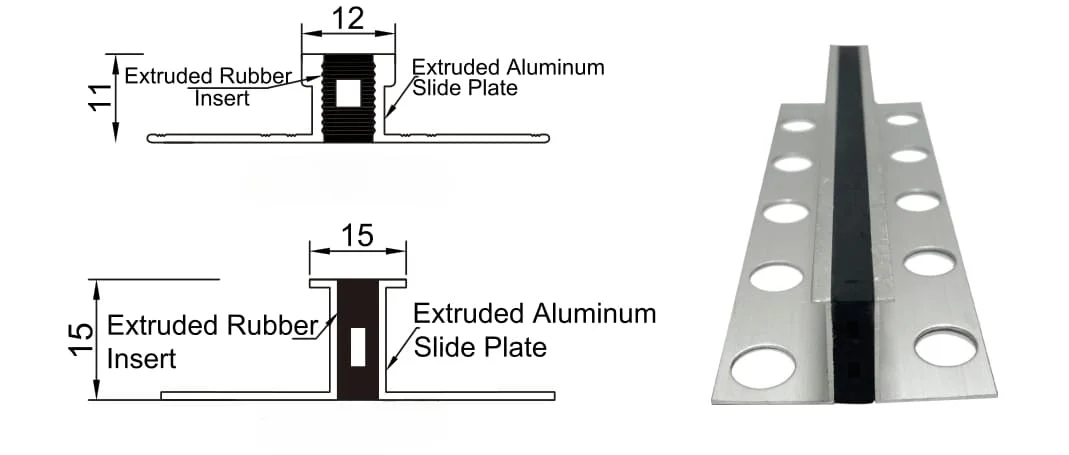
The core of a movement control joint is typically made from neoprene, a synthetic rubber known for its durability and resistance to a wide range of chemicals and detergents commonly encountered in tiled applications. This makes neoprene an ideal material for environments where frequent cleaning or exposure to aggressive substances is expected.
For adaptability to different structural and aesthetic requirements, these joints can be outfitted with slide plates made from aluminum, stainless steel, or brass. Each material offers unique benefits, such as corrosion resistance and aesthetic appeal, allowing for a tailored approach to building design and functionality.
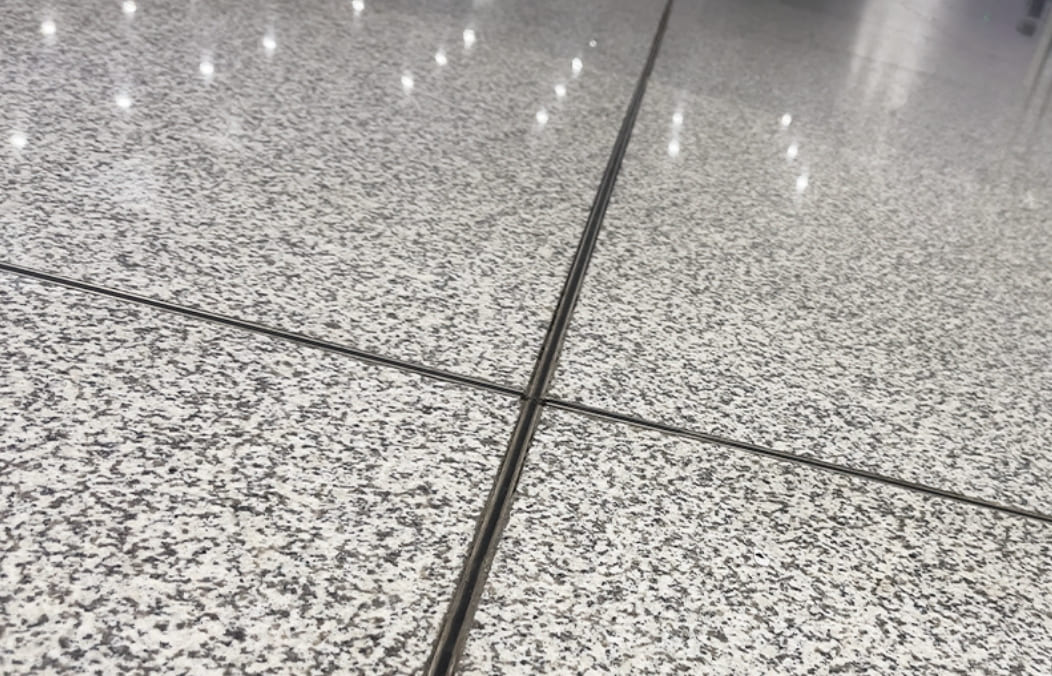
Installation of movement control joints involves securing them into the screed using perforated mounting brackets. These brackets ensure a stable and durable connection, crucial for the effective performance of the joint under varying stress conditions. Additionally, the installation process can be enhanced by incorporating insulation material as a joint filler. This not only provides extra sound insulation but also improves the thermal efficiency of the joint system.
Floor Expansion Joint
Floor expansion joints accommodate natural movements due to thermal changes, load shifts, and seismic activities within flooring systems. This category includes various specialized covers designed for different environments and needs.
1. Standard Metal Covers
Standard Metal Covers are designed with durability and ease of installation in mind. These surface-mounted covers are an economical solution for retrofit and new installations alike. Features such as serrated surfaces and beveled edges enhance pedestrian safety.
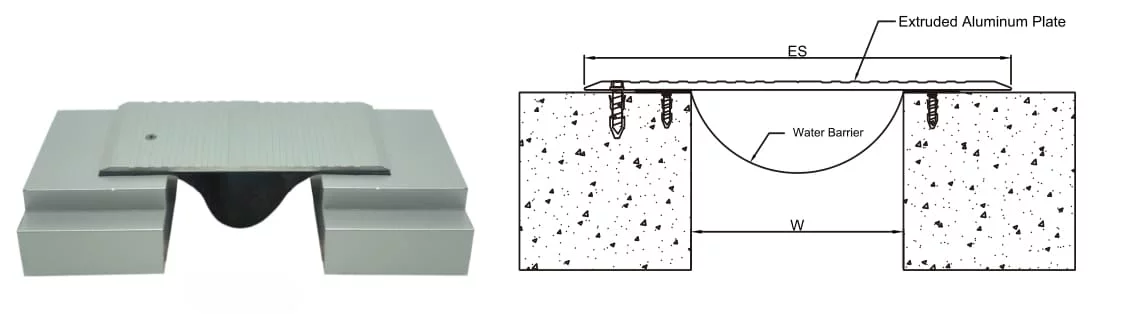
Available in materials like stainless steel and brass, and adaptable to wider widths, these covers meet a wide range of installation needs. The anodised aluminum finish not only provides durability but also complements the visual aesthetics of the installation areas. These covers are popular due to their cost-effectiveness and versatility in various architectural contexts.
2. Flush Seismic Floor Covers
These covers feature a POP UP system and a centering bar/compression spring assembly, which repositions the cover after seismic activities.
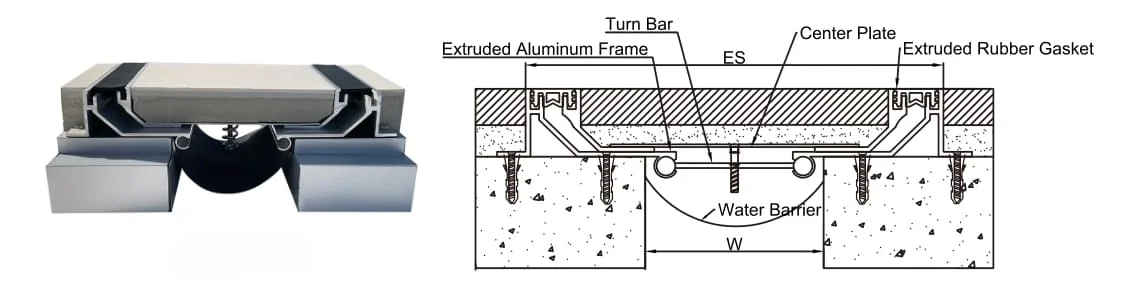
Suitable for high-grade stone floor finishes such as marble, granite, limestone, and pavers, these covers have a dual seal design to manage movement ranges while maintaining minimal sightlines. The modular pan design reduces deflection and cracking, ensuring the cover integrates smoothly into the flooring system.
3. Flush Thinline Floor Covers
Designed for smaller joint widths, these covers offer a recessed design that reduces visibility. They include a flexible seal that maintains flexibility while ensuring a secure fit, adaptable to various floor finishes.
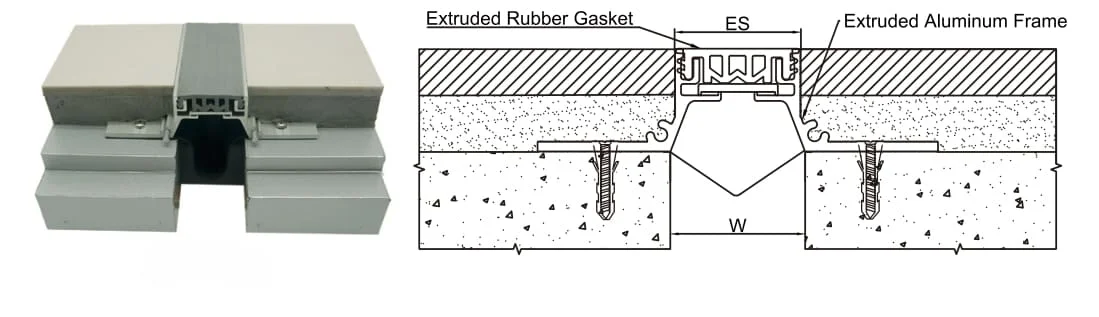
An optional vapor barrier can be integrated to enhance moisture control, adding to the functionality of the covers in different settings.
4. Flush Twinline Floor Covers
Equipped with a centering bar or clip system, these covers handle significant movement ranges and are suitable for environments with moderate to heavy foot traffic.
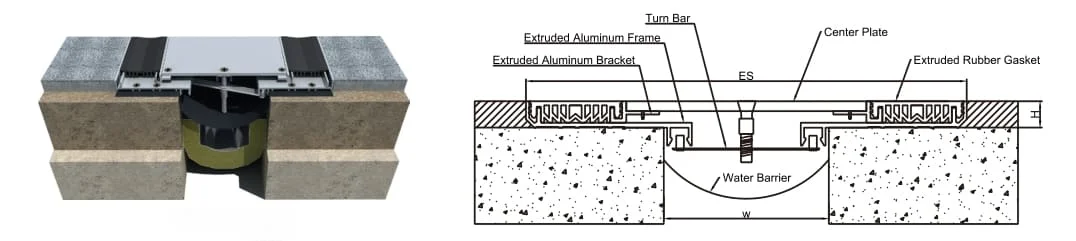
The dual seal design and snap-fit assembly make them suitable for carpet, vinyl, or ceramic tile finishes. The extruded aluminum frame contributes to the durability and visual appeal of the installation.
5. Heavy Duty Floor Covers
These covers are designed to withstand significant loads, suitable for areas with vehicular traffic like parking garages. They feature compression EPDM seals, sound dampening pads, and stainless steel springs to enhance functionality.
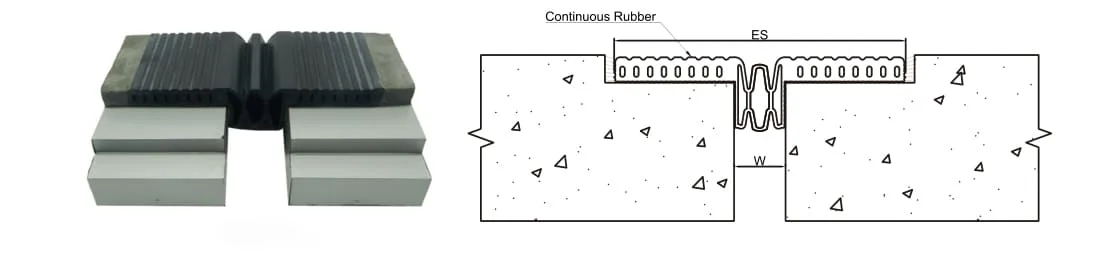
The design elements make these covers watertight, fire-rated, and chemically resistant, meeting the requirements of industrial and commercial settings.
Each type of floor expansion joint cover is tailored to specific applications, ensuring that they meet the functional requirements and align with design aesthetics.
6. Heavy Duty Metal Covers
Heavy Duty Metal Covers incorporate a centering bar system and are rated for high load bearing, making them suitable for vehicular traffic. These systems are engineered for both pneumatic and solid tires and are an ideal choice for parking garages, warehouses, and areas requiring trolley access.
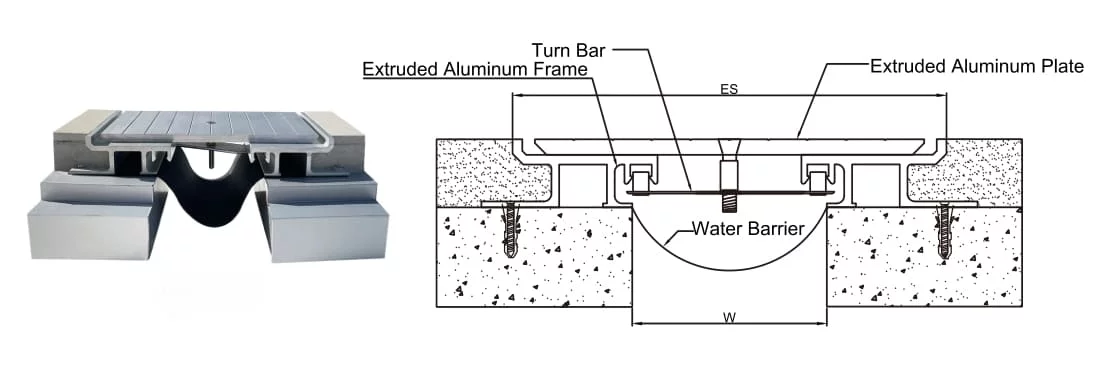
The design includes various options for cover plates, including aluminum, stainless steel, and galvanized steel, ensuring durability and aesthetic options to match different environments. The centering cover plate effectively conceals screw fixings, contributing to a cleaner and more attractive surface.
7. Lock Metal Floor Covers
Lock Metal Floor Covers feature a glide plate system which facilitates simple installation. The architectural aluminum frames and covers can be either exposed or recessed, depending on design requirements.
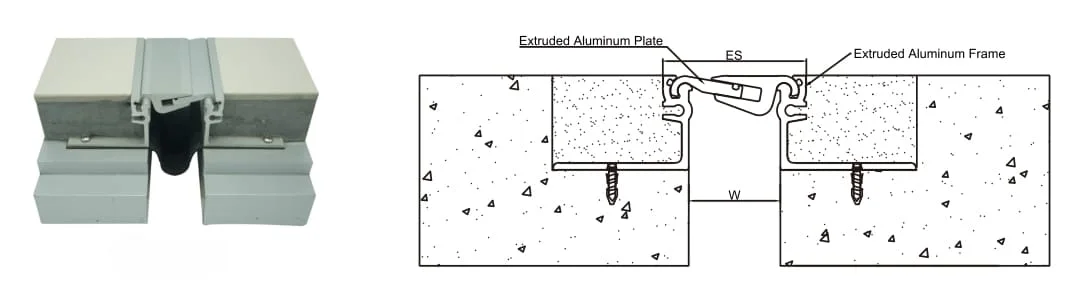
The NO-BUMP configuration ensures compliance with safety standards, making these covers suitable for a variety of floor finishes including carpet, vinyl, and ceramic tile. This design is favored for its combination of durability and ease of installation, enhancing both functionality and aesthetics.
Wall Expansion Joint
Wall expansion joints are integral components of a building's structure, designed to safely absorb and accommodate thermal and structural movement between sections of walls. These joints prevent the transmission of compressive forces that can lead to cracking or structural damage, particularly in larger buildings or structures subject to varying environmental conditions.
1. Standard Metal Wall Covers
Standard Metal Wall Covers accommodate joint widths ranging from 75mm to 500mm. These covers feature a glide plate and centering bar system, making them suitable for both interior and exterior walls, as well as ceilings. The recessed frame option is designed specifically for drywall installations but can also be surface mounted, providing flexibility in application.
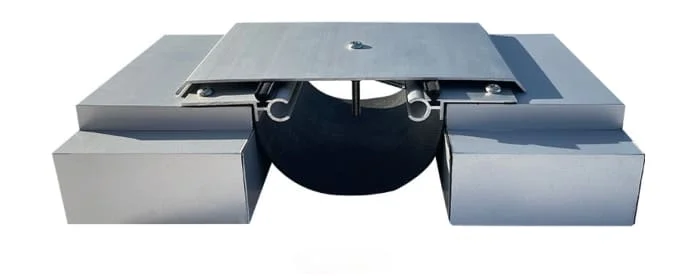
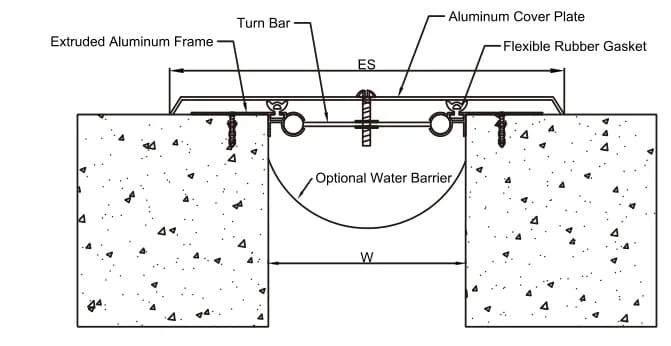
Material options include anodised aluminum, sprayed aluminum, stainless steel, and brass, each offering enhanced durability and a visually appealing finish. These covers are designed to handle significant movement, ensuring longevity and maintaining aesthetic integrity across various wall finishes.
2. Lock Metal Wall Covers
Lock Metal Wall Covers are designed for narrower joint widths of 50mm to 200mm and are suitable for both interior walls and ceilings. They feature a glide plate system and a snap-fit cover design, which facilitates easy on-site assembly without exposed fasteners, ensuring a clean and attractive finish.
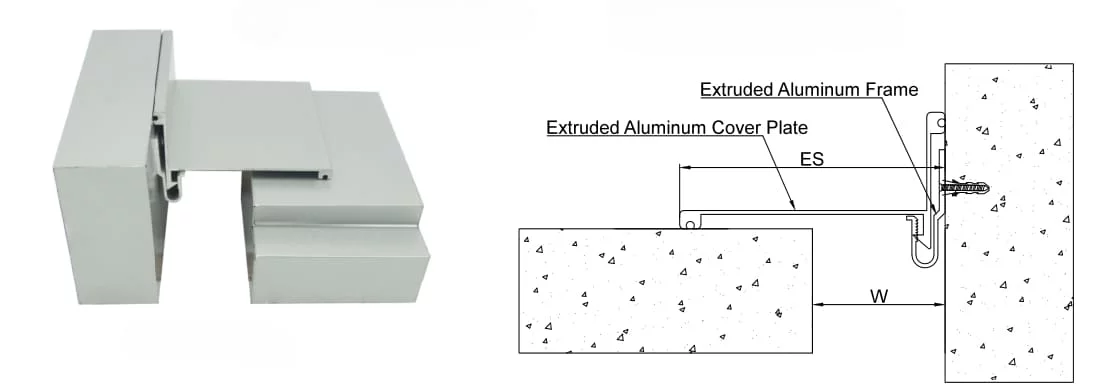
These covers are also available for a wider range of joint widths up to 500mm and include options for recessed frames, enhancing their versatility. The absence of exposed fasteners not only improves aesthetics but also contributes to the durability of the installation.
3. Flush Rubber Wall Covers
Flush Rubber Wall Covers are engineered to accommodate joint widths between 50mm and 250mm and are designed for multi-directional seismic movement. These covers feature unique seal barbs that secure engagement in the frame, making them ideal for various decorative levels, including coating and tile.
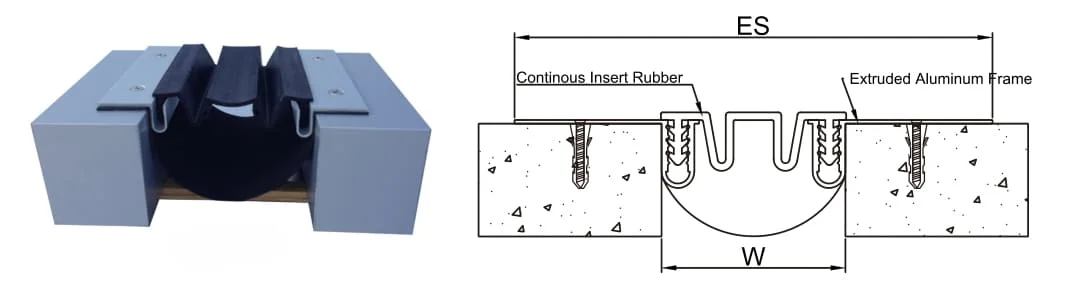
The rubber material is resistant to UV rays, ozone, acid rain, and extreme temperatures, ensuring durability in diverse environments. The seals are available in both standard and custom colors, and the continuous lengths available simplify installation and maintenance. These covers are particularly noted for their ability to remain flat and resist sagging, enhancing both function and form.
4. Curtain Wall Covers
Curtain Wall Covers are designed to manage large joint widths and significant movement capacities, making them ideal for applications where concealment of the joint is desired.
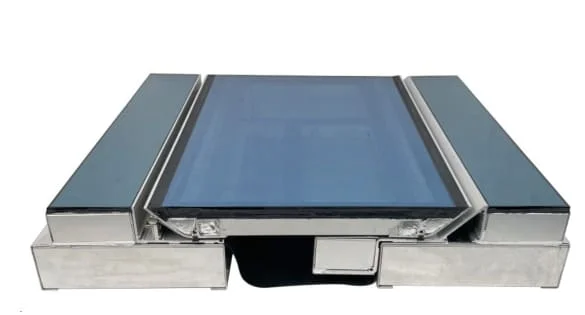

They feature a magnet system that automatically returns the joint cover to its nominal position following seismic events, while safety cables are included to prevent damage to surrounding finishes. This design is useful for maintaining the integrity and aesthetic of curtain walls, particularly in high-seismic zones.
5. Ceiling & Interior Wall Covers
Ceiling and Interior Wall Covers are designed to integrate into various interior design schemes while accommodating the necessary movement within the building structure. These covers are typically used where the aesthetics of interior spaces are a priority, offering solutions that blend functionality with design.
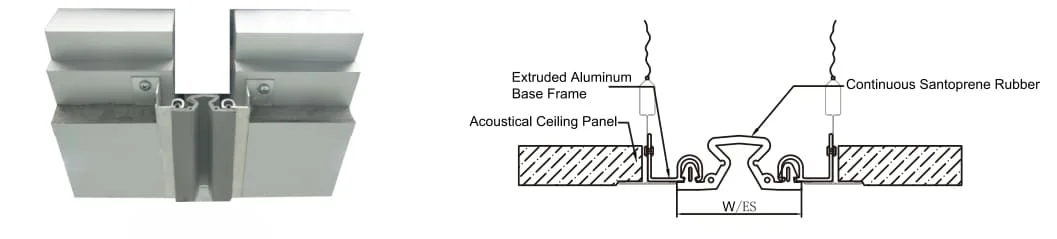
They are constructed to be compatible with various architectural details and finishes, ensuring that they contribute to the overall aesthetic rather than detract from it.
Roof Expansion Joint Covers
Roof Expansion Joint Covers are designed for applications spanning from one roof area to another, accommodating joint widths ranging from 50mm to 500mm. These covers feature Neoprene weather washers that prevent leaks at points where fasteners penetrate the frames or covers. Additionally, the use of gasketed fasteners enhances the system's ability to resist both water and air passage, providing a more secure and durable seal.
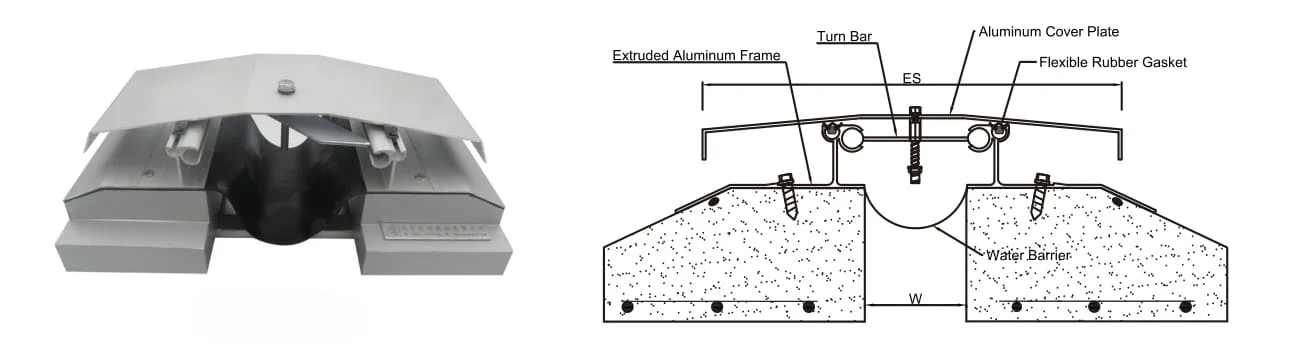
The surface mount system of these covers is specifically designed to accommodate uneven expansion joint widths, offering a versatile solution adaptable to various structural conditions. Material options for these covers include anodised aluminum, sprayed aluminum, stainless steel, and brass, providing choices to match specific durability requirements and aesthetic preferences.
Aluminum covers can also be engineered to resist environmental loads such as snow and wind, making them suitable for geographic areas prone to harsh weather conditions. This capability ensures that the roof expansion joint covers not only maintain a waterproof and airtight seal but also support the overall structural integrity of the building envelope.
Water Barrier
The Water Barrier is constructed from high-quality EPDM, providing effective waterproofing capabilities. The MSRG system is a continuous EPDM high-performance fabric reinforced rubber gutter system, which includes an optional flexible drain tube assembly for enhanced waterproofing of expansion joints. This system is particularly beneficial as a secondary waterproofing measure to protect occupied commercial spaces. Due to its fabric reinforcement, the MSRG gutter minimizes material elongation, making it a cost-effective solution for the remedial repair of leaking expansion joint systems.
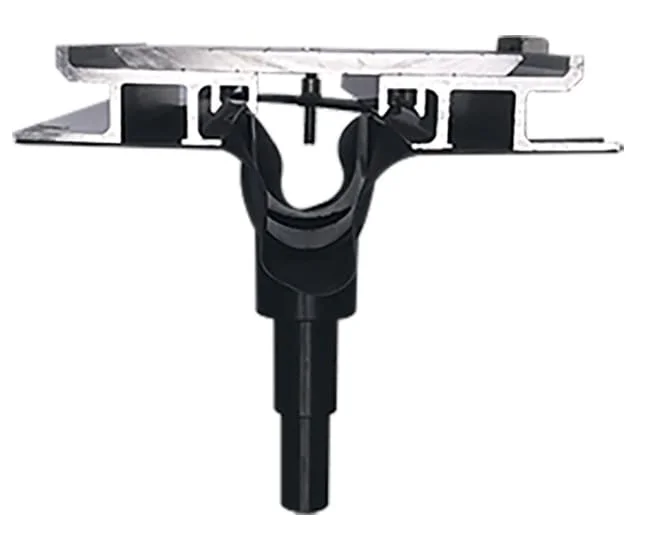
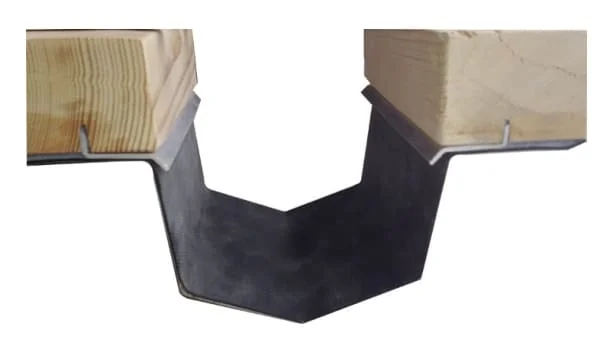
Additionally, the stainless steel rhone designed by Awisdom Tile Accessories addresses situations where front-side waterproofing is challenging. This design incorporates a strip of stainless steel rhone along the back surface, which not only redirects water flow into the rhone but also includes a water barrier within the stainless steel rhone itself. This triple-layer barrier system is engineered to provide optimal waterproofing by preventing water from flowing along unintended paths and ensuring it is directed into appropriate drainage channels.
Fire Barrier
The Fire barrier consists of stainless steel foil and aluminium silicate. It is specifically designed for use in nominal floor and wall expansion joints and is fully compatible with corresponding expansion joint covers.
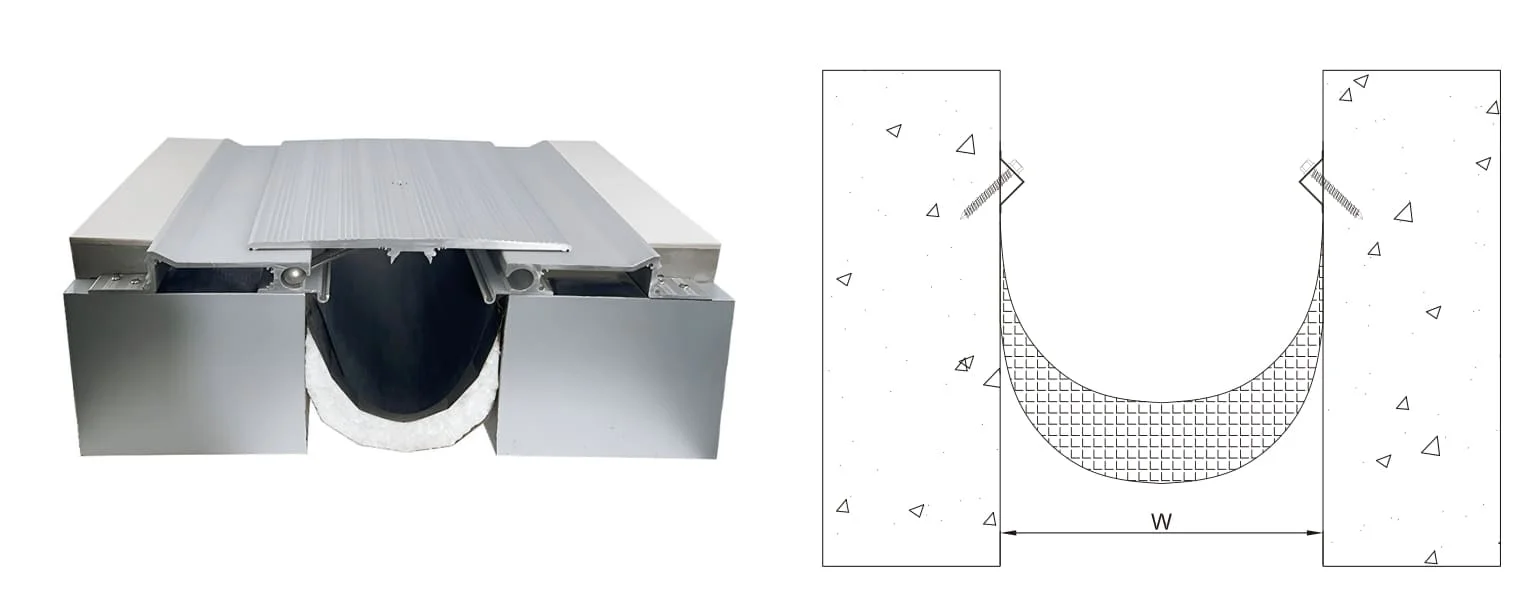
The fire barrier has been rigorously tested according to ASTM E 119 and ASTM E1966 standards, demonstrating its capability to provide fire endurance ratings of 2, 3, and 4 hours. This performance makes it an essential component in enhancing the fire safety of buildings, ensuring that expansion joints contribute to rather than detract from the overall fire resistance of the structure.
Where should the movement joint be placed?
Basic Types and Placement Principles
There are three basic types of joints: construction joints, connection (or isolation) joints, and movement (or expansion) joints. Movement joints, in particular, are crucial as they accommodate expansion and contraction, preventing damage. The complexity of the structure often dictates the complexity and placement of these joints.
Concrete Constructions
In concrete structures, the types of joints include construction, expansion, contraction, and isolation joints. Expansion joints in buildings longer than 45 meters should include at least one expansion joint, with recommended spacing being 30 meters apart. These joints are formed by providing a gap between building parts to relieve stress.
Tile Installations
For tile and stone installations, the Tile Council of North America (TCNA) recommends placing an expansion joint every 8 to 12 feet in each direction, with additional joints at all perimeters, changes in plane, and transitions to other surfaces. This spacing is designed to accommodate the natural expansion and contraction of ceramic tile and stone materials.
Timber Frame and Light Gauge Steel Frame (LGSF) Structures
In timber frame buildings, movement joints are concentrated at floor zones where the majority of movement occurs. For LGSF structures, movement joints should be located under openings, eaves, and verges to account for different movement rates compared to external cladding.
Rendered Walls
Movement joints in rendered walls should carry through from the substrate to the face of the render to reduce the risk of damage. For render onto masonry, any substrate movement joints should be continued through to the render. When rendering onto timber/steel framed structures, vertical movement joints should be provided at maximum 5m centres.
Considerations for Differing Materials and Changes in Height
Accommodating movement where differing materials abut each other or where there is a significant change in height in the building elevation is crucial. Movement joints or bed joint reinforcement may be required in these instances to manage the differential movements effectively.
How to Install Movement Joints in Tile Floors
To install movement joints in tile floors effectively and avoid common issues such as cracks and loose tiles, a precise and well-planned approach is required. Here's a detailed method based on industry practices and expert advice from various sources:
- Prepare the Area: Ensure that there is a gap between the tile and any adjoining walls or hard surfaces. This perimeter joint should be at least 1/4 inch wide to allow for tile expansion without causing damage. For tiles abutting different materials like hardwood floors, fill this gap with 100% silicone sealant for flexibility.
- Identify Field Movement Joint Locations: For interior areas, place movement joints every 20-25 feet. In areas exposed to direct sunlight or outdoors, these should be placed every 8-12 feet. Ensure that the joints extend from wall to wall for effectiveness, and consider placing them in doorways to minimize visibility.
- Installing Movement Joints:
- Clean the Space: The gap designated for a movement joint must be free of thinset or any other materials down to the substrate.
- Tape Off the Area: Apply painter's tape along both sides of the joint to keep the area clean during sealant application.
- Insert Backer Rod: Place an appropriate-sized foam backer rod into the joint to support the sealant. This also enhances the performance of the joint.
- Apply Sealant: Fill the joint with a suitable sealant, such as 100% silicone or a sealant meeting ANSI C-920 standards, that matches the color of your grout. Ensure the sealant covers the backer rod completely and smooth it out for a clean finish.
- Final Touches: Once the sealant is applied, remove the painter’s tape to leave a neat joint. If using silicone, smoothing it with a sealant tool or even a plastic spoon can help achieve a professional finish.
- Choosing the Right Movement Joint: Movement joints come in various designs suitable for different applications, including intermediate and perimeter locations. They are available in materials like aluminum, stainless steel, and PVC, with infills of flexible materials like neoprene or polyurethane for specific purposes. Selecting the correct joint profile and its placement should be planned before the tiling installation to accommodate predicted movement.
- Critical Considerations for Placement: Movement joints must align with any existing structural expansion joints in the subfloor. They are crucial at changes in the substrate, perimeters of large tiled areas, and around fixtures. The general guideline suggests a maximum bay size of 40 sq.m. for tiled floors bounded by movement joints, with intervals between joints depending on factors such as substrate, underfloor heating, and exposure to sunlight.
Remember, the installation of movement joints is a crucial step in ensuring the durability and aesthetic quality of your tile installation. Following these steps and adhering to industry standards can help prevent potential issues like cracking or debonding due to thermal expansion, mechanical forces, or other stresses on the tiled surface.
FAQ about Movement Joint
What is a movement joint vs expansion joint?
Movement joints and expansion joints are essential components in construction to accommodate the dynamic nature of materials and structures. Movement joints, also known as isolation joints, are specifically designed to allow for movement between two surfaces, such as where a tile floor meets a wall or another fixed structure. Their primary role is to prevent stress from structural movement from being transferred to the tile installation, which could otherwise result in cracking or dislodgement of tiles over time.
Expansion joints, on the other hand, are constructed to manage the expansion and contraction of materials due to changes in temperature or humidity. These joints are installed at specific intervals across a tile floor and are designed to permit movement in all directions, thereby preventing the flooring from buckling or cracking as a result of changes in the subfloor or the surrounding environment. While movement joints are typically narrower and filled with a flexible sealant to accommodate movement in one direction, expansion joints are broader and filled with a compressible foam material to allow for multidirectional movement.
Why do bridges need expansion joints?
Bridges are subject to various forces and environmental conditions that cause them to expand and contract. Expansion joints are crucial in bridge construction as they accommodate the thermal expansion and contraction of materials, absorb vibrations, and allow for soil movements due to seismic activities or ground settlement. These joints are placed between sections of bridges to prevent expansive cracks and ensure structural integrity and safety under changing temperatures and mechanical stresses.
Expansion joints in bridges are designed to withstand axial (compressive), lateral (shear), or angular (bending) deflections, ensuring that the bridge can adapt to temperature variations, loads, and other influences without suffering damage. They can be made from various materials, including metal (often called bellows type) and non-metallic materials like rubber or composite layers, depending on the specific requirements of the bridge and its environment.