Rubber cement can dry to the touch in just one minute when conditions are ideal. The drying process isn't as simple as you might think. Standard rubber cement needs 10-15 minutes to become touch-dry, while quick-drying versions set within 5-10 minutes.
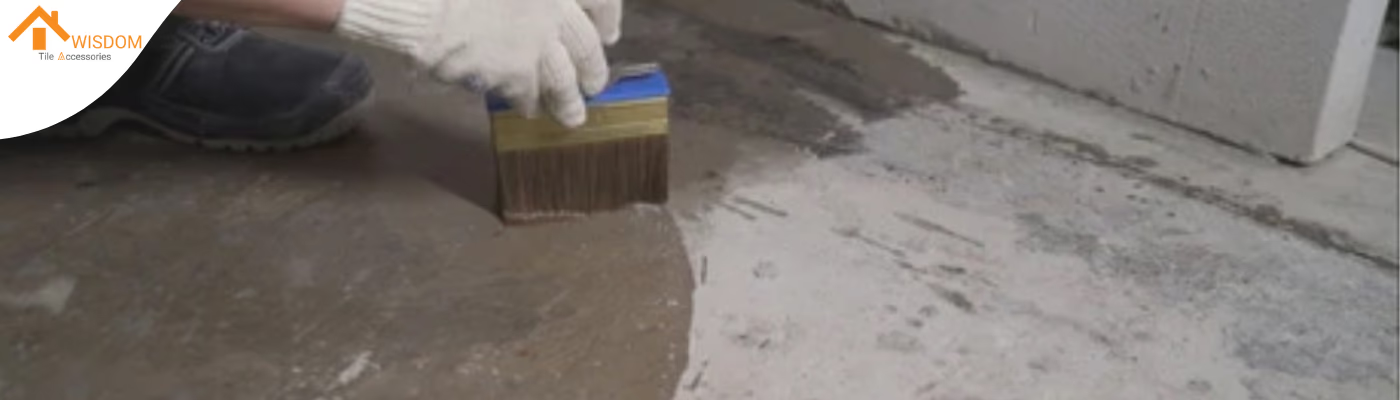
How Long Does Rubber Cement Take to Dry
The drying time varies by a lot depending on several factors. Temperature, humidity, and the thickness of application are vital elements that determine how long the cement takes to cure. Quick-drying formulas need 30 minutes to 1 hour to reach full bonding strength. Industrial variants take up to 24 hours for complete curing. This piece explores these factors that affect rubber cement's dry time and offers practical guidelines to help you achieve the best bonding results.
Understanding Rubber Cement Composition
Rubber cement's drying characteristics depend on its chemical components. A fluid adhesive solution emerges when manufacturers mix unvulcanized rubber with organic solvents. The solvent base comes from a mixture of 70-90% heptane or hexane with 1-15% isopropyl alcohol or ethyl alcohol.
Chemical Components and Their Role in Drying
Elastic polymers and solvents are the foundations of rubber cement. Natural rubber comes from the Hevea brasiliensis tree and goes through high-temperature processing to create the solid material. The solvents - acetone, hexane, heptane, or toluene - keep the rubber fluid enough to apply. The cement's solidification time depends on how quickly these solvents evaporate.
Different Types of Rubber Cement
Rubber cements come in three distinct categories based on their composition and use:
- Standard Rubber Cement: Contains basic rubber-solvent mixture, drying to touch in 5-10 minutes
- Acid-Free Rubber Cement: Made for archival purposes to prevent material degradation over time
- Industrial Rubber Cement: Offers improved bonding strength and needs up to 24 hours to cure completely
How Vulcanization Affects Drying Time
Vulcanization significantly affects rubber cement's drying and curing process. This chemical process creates cross-links between polymer chains that strengthen the final bond. Sulfur chloride, when used as a vulcanizing agent, allows the cement to cure in minutes without heat.
Different formulations use different vulcanization mechanisms. Heat-reactive rubber cements contain accelerators that speed up vulcanization at specific temperatures. Zinc oxide and other activators improve the vulcanization rate, which changes the overall drying time.
Factors Affecting Rubber Cement Dry Time
The drying time of rubber cement depends on both environmental conditions and how you apply it. You'll get the best bonding results by knowing how these factors work together.
Temperature and Humidity Impact
Temperature makes a big difference in how rubber cement dries. You'll want to work in temperatures between 65°F to 110°F (18°C to 43°C). The right temperature matters because:
- Below 65°F: The curing process slows down by a lot
- 65°F - 80°F: Best temperature to store it
- Above 110°F: The cement might cure too early
Humidity levels change how well the adhesive works and how fast it dries. High humidity can create a moisture barrier between the surface and adhesive that weakens the bond. The cement usually takes 15-20 minutes to dry in normal conditions. This time can get much longer in humid environments.
Application Thickness Considerations
The thickness of your rubber cement layer will change your drying time. Thicker layers need more time because solvents take longer to evaporate from deeper inside the material. The solvents have to travel further to escape when you apply thicker layers.
You'll get the strongest bond with an even coat of adhesive. A glossy surface tells you that you've applied enough adhesive. Porous surfaces work better with several thin coats instead of one thick layer.
Surface Material Effects
Each substrate material reacts differently with rubber cement, which changes both how well it sticks and how long it takes to dry. The way you prepare the surface is vital - cleaning, roughening, and removing grease will affect how strong the final bond becomes.
Metal surfaces need a roughness between 150-250 microinches to stick properly. Materials that can absorb the cement might need extra coats, and you'll have to let each layer dry completely.
The surface temperature can change local drying speeds. Metal surfaces handle heat differently than wood or plastic, which changes how the cement dries. You should keep the surface temperature steady while it cures to get an even bond.
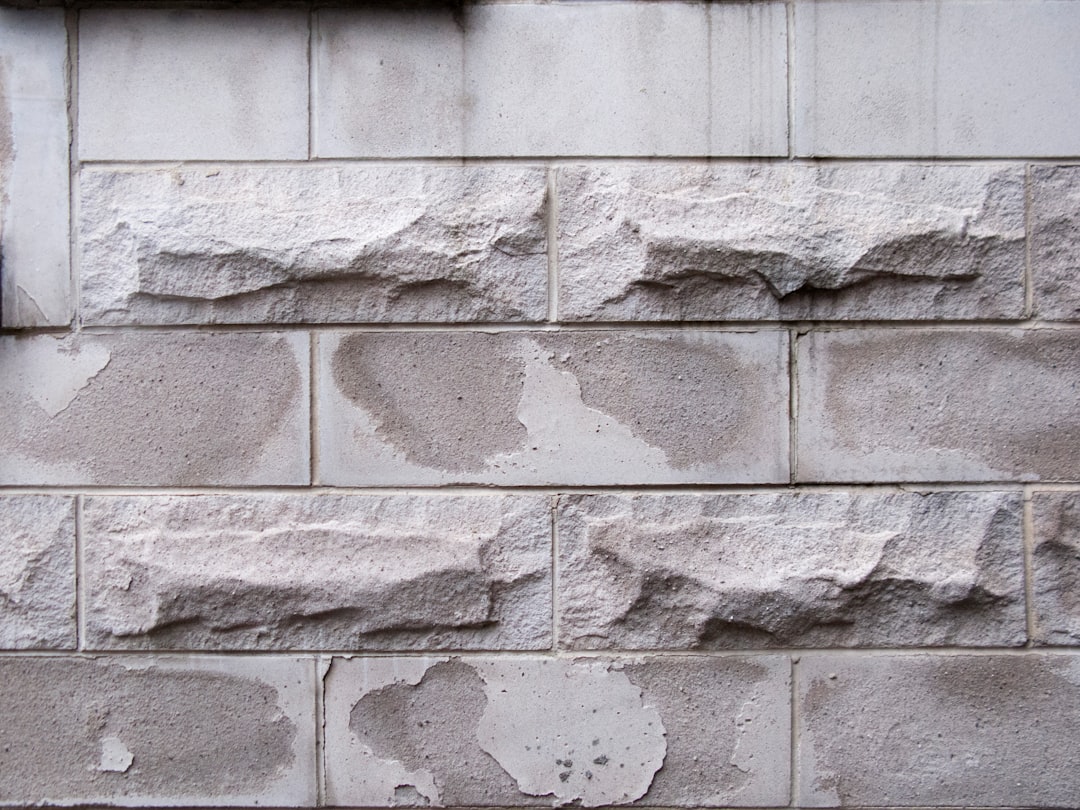
Standard Drying Time Guidelines
The right drying time is key to getting the best bonds with rubber cement. Different types have their own set times that work best for specific uses.
Quick-Set vs Regular Formula Drying Times
Quick-set rubber cement dries amazingly fast and becomes touch-dry in 5-10 minutes. Regular formulas take 10-15 minutes to reach the same touch-dry state.
Formula Type | Touch Dry | Initial Bond | Full Strength |
---|---|---|---|
Quick-Set | 5-10 min | 30 min | 1 hour |
Regular | 10-15 min | 1-2 hours | 24 hours |
Industry-Specific Drying Requirements
Rubber cement with volatile solvents used in tire repairs dries in just one minute when conditions are hot and dry. You'll still need to wait 15 minutes before testing the pressure. We used rubber roofing applications that need longer drying times to arrange joints and smooth seams before the adhesive sets.
Full Cure vs Touch Dry Timeline
The difference between touch-dry and full cure states is vital to bond strength. DAP WELDWOOD Contact Cement gives you 2 hours of open time after it becomes tack-free. The maximum holding strength takes 7 days to develop fully.
For industrial applications:
- Standard rubber cement becomes touch-dry in 10-15 minutes
- Acid-free variants need 15-30 minutes before handling
- Complete curing takes up to 24 hours, depending on how thick you apply it
Temperature is a big deal as it means that keeping it between 65°F to 120°F will give a proper drying time. Let bonded assemblies cure for 72 hours before exposing them to direct sunlight or temperatures above 150°F to get the best results.
Optimal Application Techniques
The right application techniques make a huge difference in rubber cement drying times. We focused on surface preparation, tool selection, and ways to avoid common mistakes to get the best results.
Surface Preparation Methods
Strong bonds start with careful surface prep. The first crucial step is degreasing with volatile solvents like toluene, acetone, or methyl ethyl ketone. These remove surface contaminants. Good ventilation helps solvents evaporate and keeps the workspace safe.
Metal surfaces need a surface roughness between 150-250 microinches for the best adhesion. A proper surface prep follows these three steps:
- Vapor degrease/clean/rinse with appropriate solvents
- Immerse in fresh solvent bath for washing
- Complete final rinse and dry thoroughly
Tools and Application Strategies
Your choice of application tools affects the cement's drying time and bond strength. Acid brushes work great for precise spots, while spreaders handle larger areas better. Good brush care leads to longer tool life and even application.
The coating thickness needs careful control - thin, even layers work best. Here's how to apply rubber cement properly:
- Apply over scrap paper to manage excess
- Use smooth, consistent strokes
- Let each coat dry fully
Dual-surface applications need both surfaces coated. Wait until the glue becomes tacky, usually 2-3 minutes. This creates stronger bonds and speeds up drying.
Common Application Mistakes
Knowing what can go wrong helps create better bonds with faster drying times. Many people use too much adhesive. Industry experts say excess rubber cement makes adjustments impossible and takes much longer to dry.
Watch out for these mistakes:
- Skipping surface prep steps
- Not reading manufacturer's instructions
- Working in poor conditions
Temperature control matters during application. Keep it between 65-75°F (18-24°C) with 50% relative humidity. A well-ventilated workspace helps solvents evaporate faster and keeps you safe.
The best results come when you avoid moving materials after the original contact. Moving them weakens the bond and extends curing time. On top of that, storing rubber cement in sealed containers prevents early drying and keeps it working consistently.
Troubleshooting Drying Issues
Rubber cement drying issues need close attention to signs and environmental factors. We focused on understanding common problems to stop bond failures and get the best adhesion results.
Identifying Improper Drying Signs
Bond defects between rubber and cement matrix demonstrate through specific visual and physical indicators. You'll spot improper drying through these reliable signs:
- Excessive penetration into substrate materials
- Formation of air bubbles or voids
- Uneven surface texture
- Incomplete bonding at edges
Vulcanization affects drying time and poor curing shows up as weaker mechanical properties and bond strength. The rubber cement might show signs of "blushing" - moisture condensing on fresh adhesive - and this needs quick action.
Environmental Challenge Solutions
Temperature and humidity affect rubber cement's drying behavior by a lot. Managing environmental challenges needs specific conditions:
Environmental Factor | Optimal Range | Solution for Issues |
---|---|---|
Temperature | 65°F - 120°F | Install drying heat tunnel |
Humidity | Low to moderate | Use hot spray method (135°F) |
Air Movement | Moderate | Ensure proper ventilation |
A drying heat tunnel right after adhesive application helps stop condensation problems. The hot spray method at 135 degrees Fahrenheit works well against moisture issues in humid places.
When to Restart Application
Some situations need a fresh start with rubber cement application. Air trapped in the adhesive tube during application makes the cement evaporate inside and loses its effectiveness. You'll need to reapply when:
- Puddling shows up in the original application
- Surface shows contamination signs
- Cement dries unevenly
- Environmental conditions change dramatically during application
Remove all previous adhesive and clean the surface well before reapplying. Fresh adhesive gives better results if bond failure happens due to poor storage or handling.
Bond interface monitoring is vital for industrial applications. Complete reapplication might be needed if too much ettringite forms and causes tensile stresses that start cracks. The application process should start over with the right environmental conditions if the rubber cement shows poor vulcanization or weak adhesion.
Solutions can seep through porous surfaces or those with voids in the microstructure and weaken the bond. Surface preparation needs another round and fresh rubber cement in these cases. High-stress applications or vital bonding needs another application right away if the first drying looks wrong to ensure the bond stays strong.
Conclusion
Rubber cement is a versatile adhesive that takes minutes to hours to dry based on conditions. Quick-set formulas dry enough to touch in 5-10 minutes. Standard versions need 10-15 minutes in the right conditions. The temperature should stay between 65°F and 110°F to cure properly, and humidity levels must remain moderate.
You need several elements to succeed with rubber cement. The surface must be clean, the application thickness correct, and environmental conditions right - these factors affect the bond strength and drying time. Understanding these basics will help you get reliable results with different materials.
There's a significant difference between touch-dry and fully cured states. You might handle the bond in minutes, but complete bond strength develops over 24 hours to 7 days. This understanding and proper troubleshooting skills will give a successful adhesive application in projects of all sizes.
Note that each application needs a different approach based on the material and environment. Your attention to surface prep, tool choice, and proper technique leads to consistent, quality results with rubber cement.
FAQs
Q1. How long does it typically take for rubber cement to dry completely?
Rubber cement usually becomes touch-dry within 10-15 minutes, but full curing can take up to 24 hours. The exact drying time depends on factors like temperature, humidity, and application thickness.
Q2. What's the best way to speed up the drying process of rubber cement?
To accelerate drying, apply thin layers, ensure proper ventilation, maintain an ideal temperature between 65°F and 110°F, and avoid disturbing the adhesive during the drying process.
Q3. Is rubber cement a permanent adhesive solution?
Rubber cement is not typically considered a permanent adhesive. It forms a flexible bond that can be removed from non-porous surfaces like glass or metal, making it suitable for temporary or repositionable applications.
Q4. How long should I let rubber cement dry when patching a tire?
For tire repairs, allow the rubber cement to dry for about 5-10 minutes before applying the patch. This ensures the cement is tacky enough for proper adhesion without being too wet.
Q5. What factors affect the drying time of rubber cement?
The drying time of rubber cement is influenced by several factors, including temperature, humidity, application thickness, surface material, and the specific formulation of the cement. Environmental conditions play a significant role in determining how quickly the adhesive sets.